An architectural innovation was opened directly at Zurich Airport last autumn: With the Circle, Japanese architect Riken Yamamoto designed his vision of a modern city with a high quality of stay - from the outside a building, from the inside a city centre in miniature on several levels, with alleys, squares and streets, with public and private spaces.
The largest Swiss building construction project with a construction volume of around 1 billion Swiss francs refers to the large-scale forms of the airport. The new building nestles on a hill that is almost circled in a circle by the airport road - hence the name "The Circle".
The Circle opened in 2020
On up to eleven floors, there is space for science and research, art and culture, shops and offices, services and healthcare projects, conferences and congresses as well as hotels. The Circle was officially opened in November 2020.
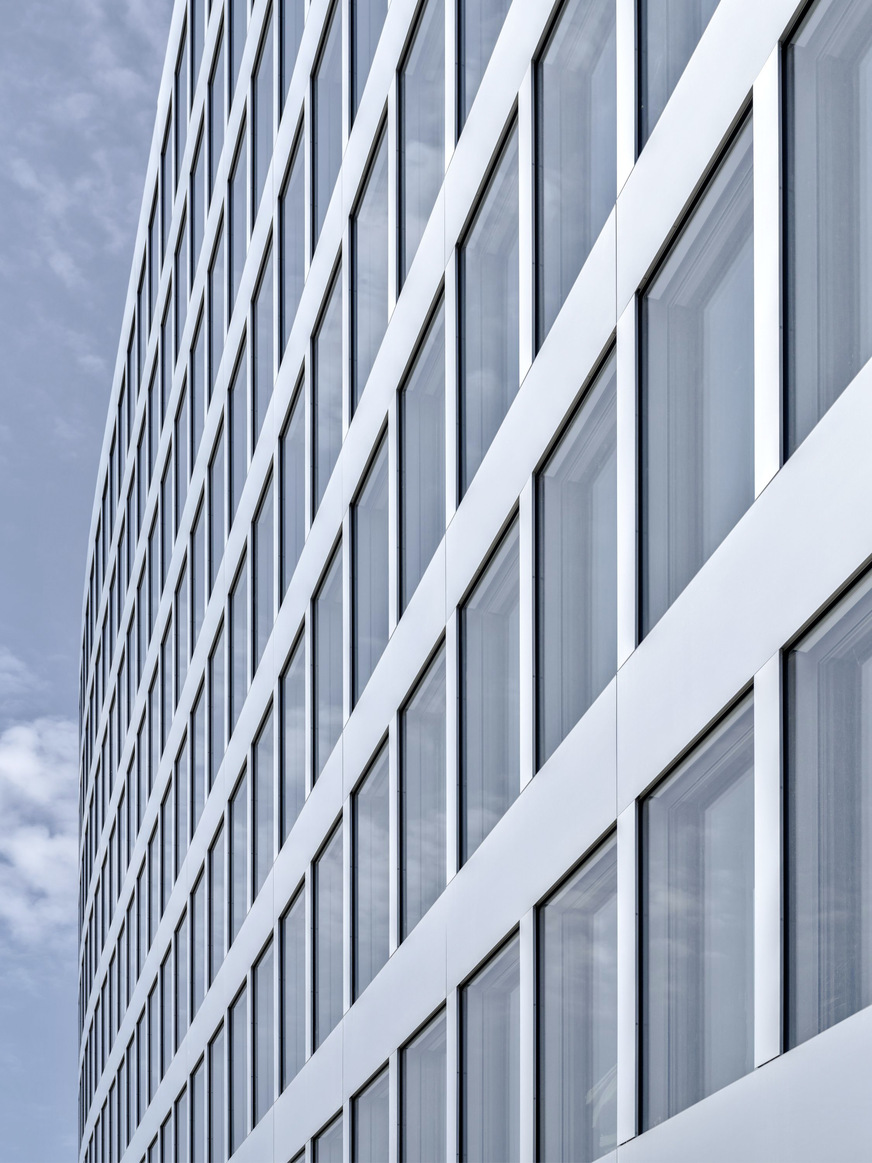
R. Dürr
The ambitious building project is certified with the highest LEED standard and Minergie. Both building standards stand for sustainability and a responsible approach to energy.
Planned as double facade
An essential component of the Circle's ambitious energy concept is the construction of the glass facade, which encloses all buildings on the outside. It was planned as a double facade in order to use the thermal buffer in the intermediate space for energy saving.
This type of facade was developed by facade specialist Josef Gartner from Gundelfingen into the so-called Closed Cavity facade (CCF), for which LSG panes Gewe-safe from Schollglas were used, among others. For the Circle, Josef Gartner installed 83,900 m2 of his climate-friendly facade construction.
Specially treated air
With the Closed Cavity facade, the 135 mm deep cavity between the two facade levels is hermetically sealed. Specially treated air is fed into the resulting closed cavities through a central supply system.
The dried and cleaned air is pre-tempered and blown into the chamber at a slight overpressure. This prevents condensation from forming on the glass panes.
See also: Almost touching the sky at Chadstone shopping centre
The outdoor climate is monitored by control electronics and the dry air production in the technical centre is controlled accordingly. In this way, the energy consumption due to heating and cooling in the building can be reduced to a minimum. With its structural-physical values, the CCF has already set new standards.
What does the safety glass from Schollglas achieve for The Circle?
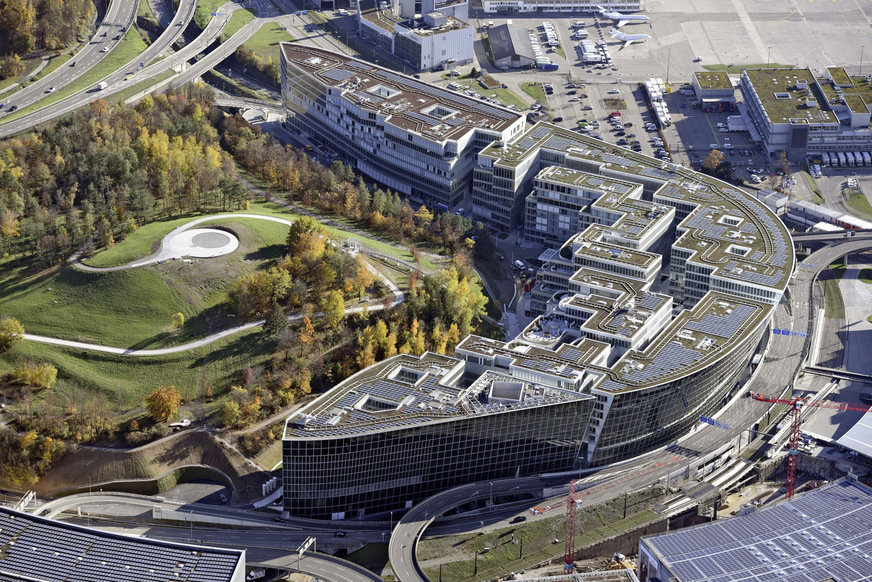
Flughafen Zürich AG
The production of the approximately 8600 facade elements for The Circle (excluding fire facades) took place in Gundelfingen, Bavaria. A special production line there ensured the highest cleanliness and precision during production. This was the only way to guarantee the perfect functioning of this special facade type. At the construction site, the elements were hung into the substructure and fixed. The glass was stored in a continuous linear dry storage system using specially extruded silicone profiles.
A closed cavity element consists of the outer impact level with laminated safety glass and the inner thermal insulation level with insulating glass. For the Circle, Gartner used safety glass of the type Gewe-safe LSG 12/2 (66.2) for the production of the CCF elements, in some cases with special requirements on the resistance to break-through in the P4A version.
Also interesting: Almost two thousand square metres of curved glass
For the inner sides of the CCF elements, the Gewe-therm heat insulation glass from Schollglas was used. For the three glass layers, 2 × 6 mm TVG in the ClimaGuard Premium2 design + 1 × 10 mm LSG were used. de (CCF), for which Gewe-safe LSG panes from Schollglas were used, among others.
For more articles like this one, make sure to have a look at our 2021 Glass Special.