A total of 149 laminates were colour-designed by artist Alexander Beleschenko for the 22 Bishopsgate building. In order to print his designs exactly on the glass, a precise printing technique was required, and at the same time the glasses had to meet high technical standards. This is where sedak was able to help and produced the safety glasses, which fully met the requirements both in terms of accurate print image and quality.
A strong, colourful counterpoint to the cool steel and glass architecture of the metropolises
Anyone walking under the glass canopies of London's 22 Bishopsgate feels as if they are in a cheerful play of colour and light. The canopies show blue, yellow, orange, red and green geometries, sometimes opaque, sometimes translucent in alternation.
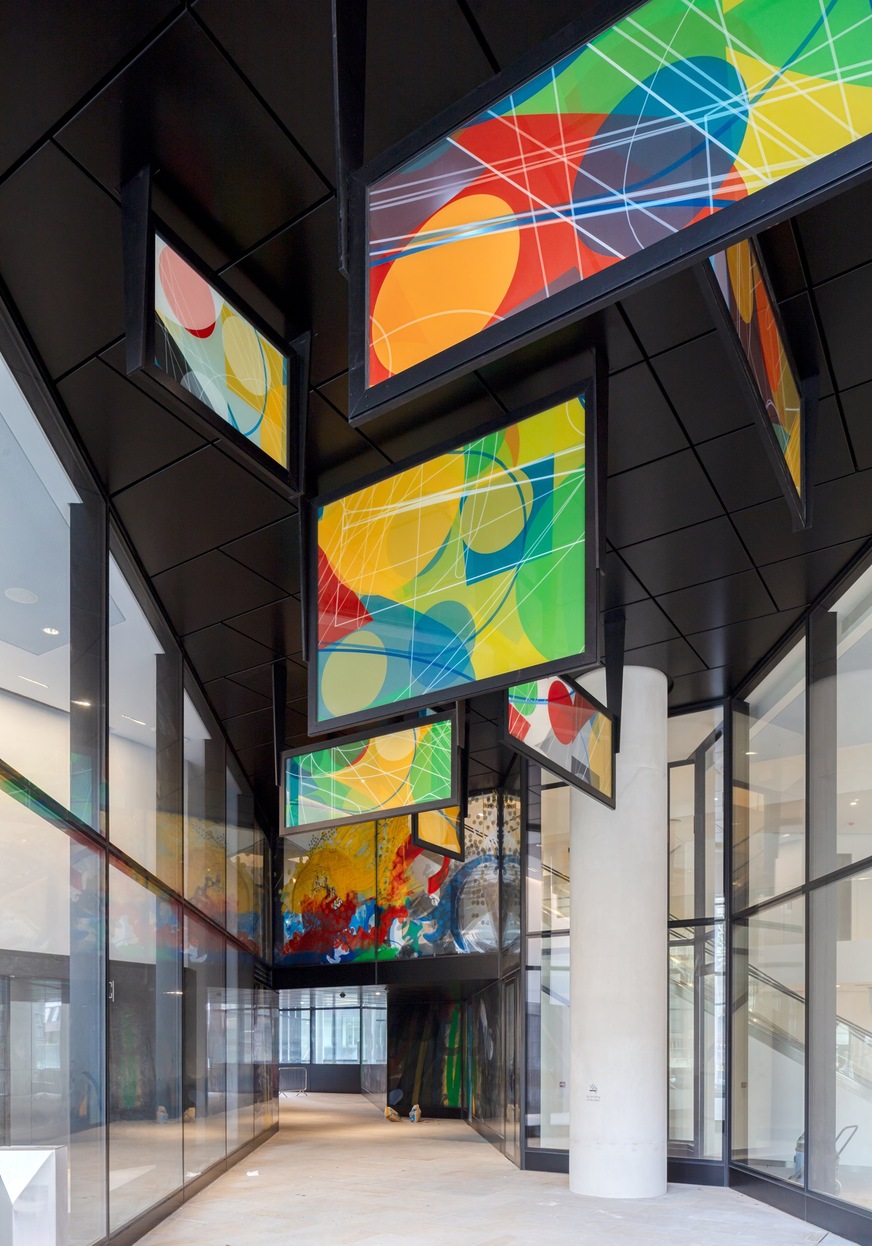
Simon Kennedy
Colour-intensive patterns, like huge brushstrokes on the glass surfaces, can also be found on the glass façade and colourful glass shapes parts of the ceilings in the passageways and serve as friendly signposts.
The lively design is reinforced by the many different glass formats, which vary in size and shape: Rectangle, trapezoid, triangle, freeform. No glass is the same, each one is unique, an imaginative work of art.
The glass was designed by the internationally renowned artist Alexander Beleschenko, who has been using the material for many years to set identity-creating architectural accents.
For 22 Bishopsgate, he was inspired by the traditional guild signs that were omnipresent in (old) London. He reinterpreted them in an abstract way, thus combining the modern with the old, as it is lived every day in the British metropolis. The symbiosis of transparency and colour glass as a roofing already poses high technical demands (e.g. risk of breakage).
What exactly did sedak contribute to the project?
The glass panes are exceptional because of the permanently colour-fast and highly precise printing, realised with ceramic digital printing in a resolution of 1080 dpi. This accuracy goes far beyond the standard. Because ceramic inks are particularly colour-stable and do not fade even under UV radiation, they are ideal for outdoor use.
See also this article: A grand tower for Frankfurt
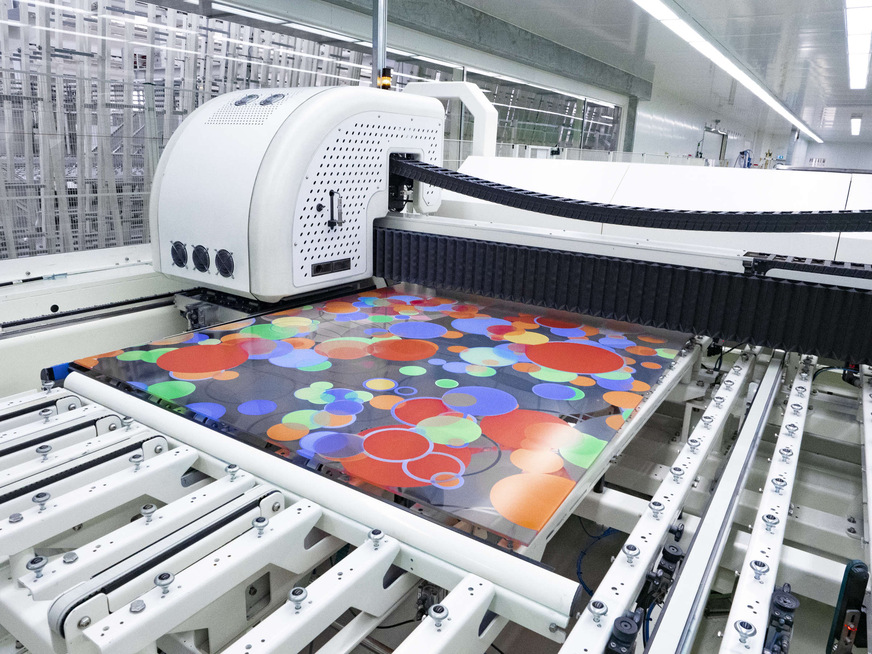
sedak
The colour fidelity and above all the extremely high precision convinced Beleschenko: he wanted his space-defining art to have just as much effect on the viewer from a distance as from up close. The production was quite simple for Beleschenko: he sent his (huge) files directly to the glass refiner sedak.
The designed panes consist of 2-fold safety glass made of 8 mm TVG (semi-tempered glass) with digital printing. In addition, there is artwork on position 3 or position 2. Since the artwork extends vertically, there is also some printed insulating glass. These are each made of two 2-ply laminates (6 mm TVG glass), filled with argon and carry the print on position 2 or position 7. sedak supplied a total of 149 laminates and 370 insulating glasses.
The artist and his work
Alexander Beleschenko knows how to design and realise art and architecture on a large scale. Nevertheless, it is also a significant moment for him to see his finally installed art - there is no way to check the complete work beforehand with these dimensions. Therefore, the close collaboration between artist and glass finisher is particularly relevant.
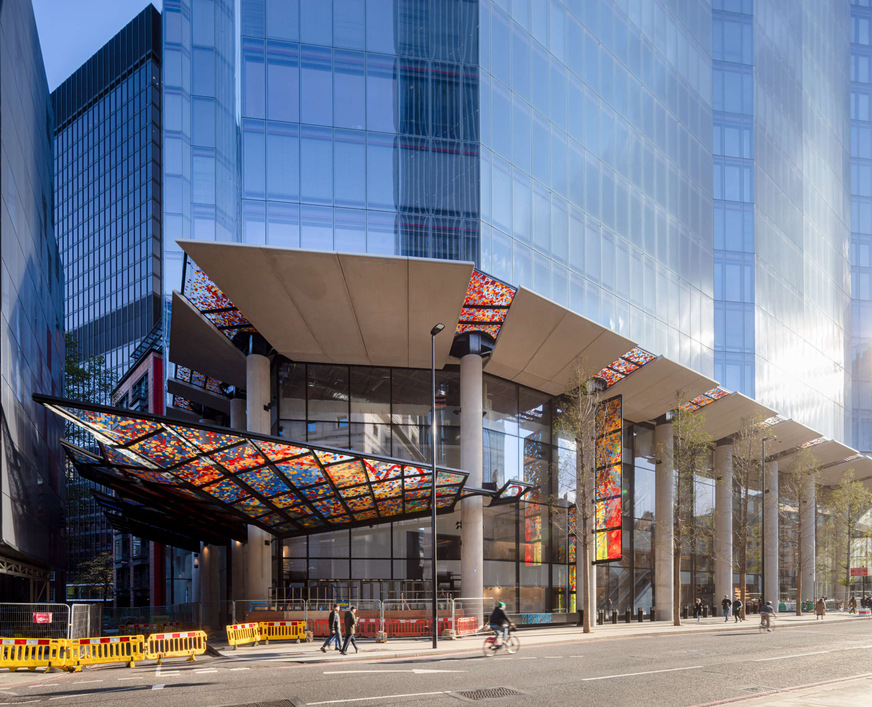
Simon Kennedy
With artistic vision, an eye for "the big picture" and know-how in dealing with the material glass and possible finishing technologies, unique works are created. When everything is perfectly realised, "in a way, you don't see the technique, you see the art", says Beleschenko - the impressive result can now be seen in London.
Ceramic digital printing, the technique for art
The glasses were digitally printed with six ceramic base colours - patterns of opaque and transparent elements, colour gradients and overlays.
This will also interest you: Rope facade for Penn Station in New York
By overlaying, a wide variety of colour nuances could be created from the basic colours - actually in different layer thicknesses. The software had to be just as powerful as the printer, the data volumes were huge: each glass is unique.