With about 120 employees and a production area of 10,000 square metres, Interpane Sicherheitsglas GmbH, based in Hildesheim in northern Germany, processes about 200,000 square metres of glass per year.
The core competence lies in the production of safety glass. In 2022, around 102 000 square metres were processed into laminated safety glass made of toughened safety glass and 98 000 square metres into monolithic toughened safety glass, generating a turnover of more than 14.5 million euros.
See also: Glass facade elements with an amazing U-value
The special decor variants such as sandblasting, screen printing, digital printing, groove cutting, as well as coloured foils and laminated photos as well as glass with alarms and also model panes in a variety of designs are part of the versatile product portfolio.
This is how the capacities in the Interpane production were expanded
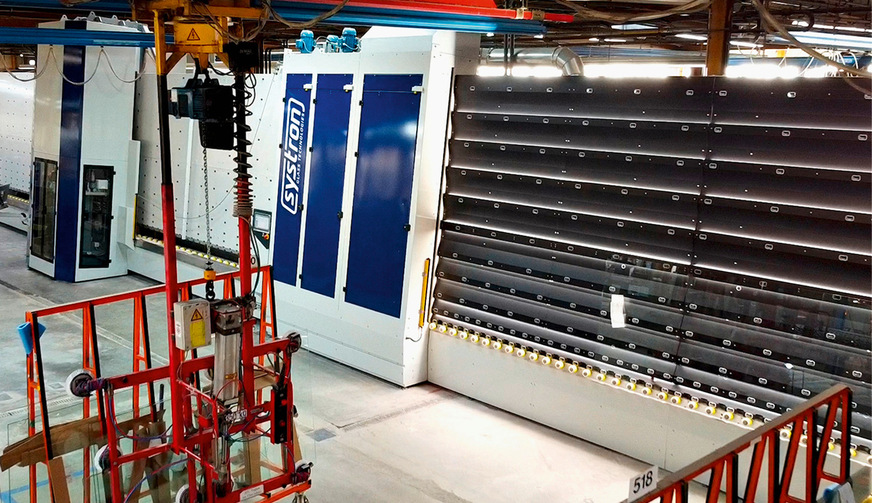
Systron
In order to avoid bottlenecks in production, plant manager Frank Matz decided to invest in a new glass processing centre in consultation with the investment managers of the AGC Group.
The specifications were very extensive: Decision criteria such as short set-up times, a high throughput, space-saving operation, ease of maintenance, high availability of spare parts, low operating costs as well as good service were ultimately decisive in the Hildesheim company's choice of the systron proHD processing centre with integrated waterjet.
"Edge processing and waterjet cutting in one system, that convinced us immediately. For our requirements, the 5029proHD is the optimal solution for glasses up to 5 m in length," says the plant manager.
Frank Matz sees the challenge in the further development of the company at the Hildesheim site among other things in the fact that it is a steadily growing operation. "We have to get by with limited space and we produce in principle batch size 1. Consequently, we need very precisely coordinated, selective automation solutions so that we don't have to rebuild the entire production," he explains.
Also interesting: AGC Interpane Group completes transfer of ownership
The installation of the 5029proHD vertical plant including the washing & drying station in February 2022 was an important step towards more efficient and space-saving production. "We previously had to use three different processing machines to produce slightly more complex glass, a horizontal processing, drilling station and the single-sided machine.
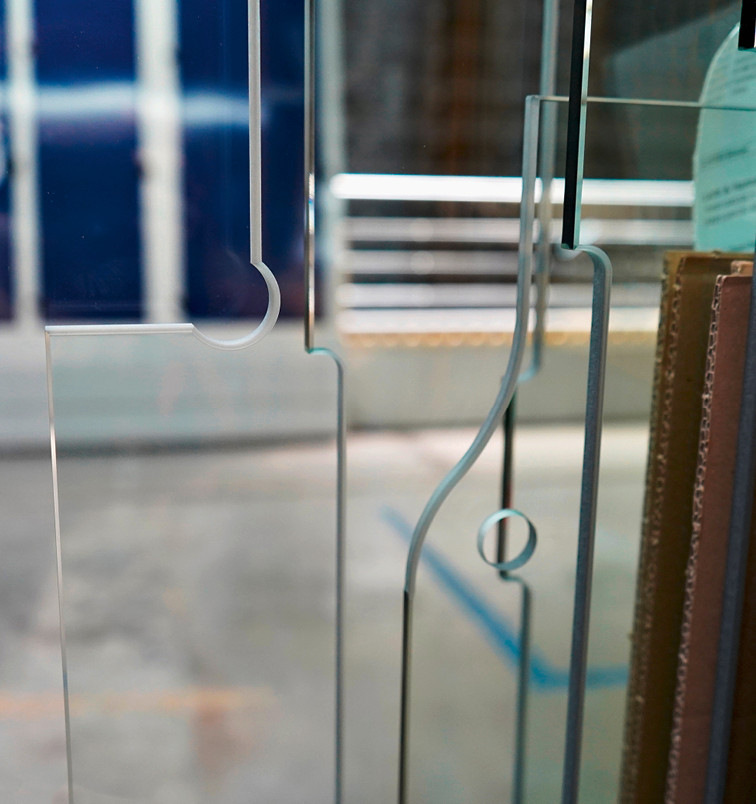
Systron
Not to mention the handling effort and the washing stations in between, this was also very time-consuming to map in the production planning system. Each step had to be timed one after the other and provided with a transition grid. Now we clamp once and get the finished glass with free shapes, holes and optimally ground and polished edges out the back. This speed optimisation was very important to us," says Frank Matz.
Fully automated interface to the ERP system
Minimising file post-processing, i.e. the processing of CAD or CAM data on the machine, was also an important optimisation point for Interpane. "The systron can do a lot and is therefore a difficult operating tool for mapping in the ERP system and for finding machining, especially because it carries out the complicated machining operations," he says.
"A little development work was necessary until everything ran smoothly, but the engineers from Albat&Wirsam and systron managed to implement our ideas with great coordination," says plant manager Matz, who is very satisfied with the result.
He adds: "I can also access various evaluations such as m² of ground or polished glass, running metres and much more from my PC. For a good overview and planning, production figures, machine utilisation, production backlogs etc. are of course essential."
Maintenance & Support
For every customer, an essential point is the machine availability and, along with it, maintenance and service. "I was immediately impressed by the machine concept, i.e. the design and maintenance accessibility," says Frank Matz. "We have now been using the system for a year and have never needed a systron technician on site. We have good maintenance in-house, in combination with systron's competent, free remote support, you can work smoothly."
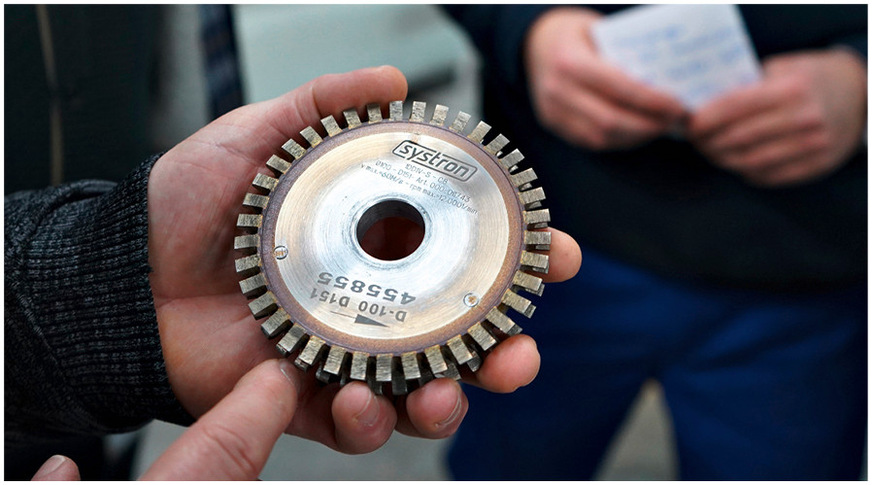
Systron
Experience with systron tools
After one year of experience, Frank Matz can also judge the tools specially developed by systron: "We work exclusively with systronTools, because here the tool is matched to the machine. Of course, there has also been a transfer of know-how from systron to Interpane in terms of machining parameters and tool selection."
Also in the Expertise series: Schwan Glas from Düsseldorf: This manufacture produces exquisite glass products
Frank Matz is also satisfied with the quality of the tools: "The feed rates and profile accuracy of these tools definitely justify the price. It's like buying the new systron system, the purchase price may seem high at first, but calculated on the running metres of a finished product and the life of the machine, the investment pays for itself very quickly."
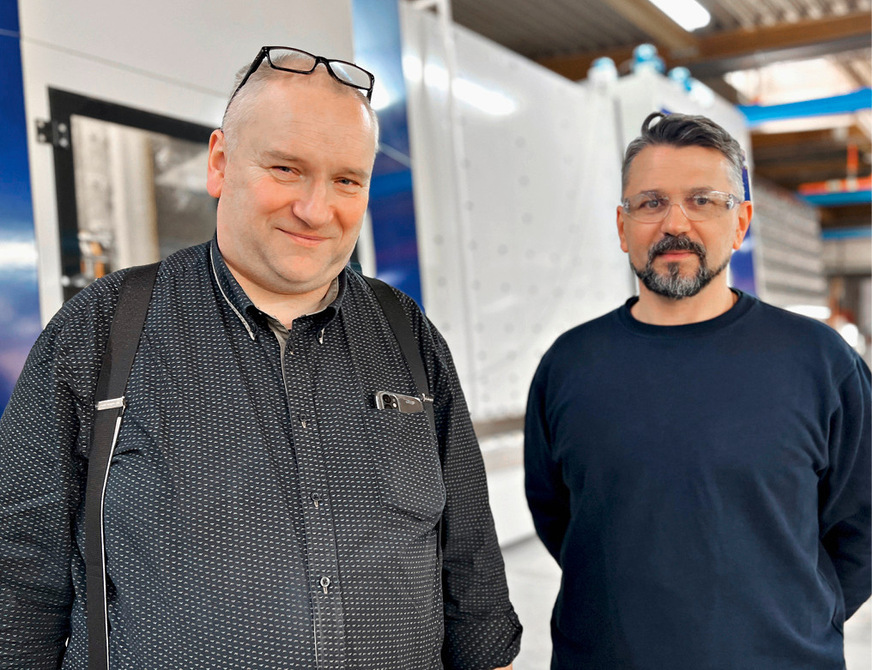
Systron