"For some problems, the scanner is the solution that a glass processor might look for elsewhere at first," says Sandra Kugler of Viprotron. Below, she and the scanner specialist's technicians have listed eight questions to consider and provides her answers to them.
1. Have you recently lost important customers and orders?
This is a sure sign that, apart from prices or inadequate service, product quality is certainly behind that of your competitors. The use of scanners helps to achieve and maintain a customer-oriented level of quality. This leads to satisfied customers and they stay, even if you are not the supplier with the lowest prices.
The same applies to the acquisition of new customers. Delivery reliability and product quality are the decisive parameters here. Just being cheap is not an alternative, because if you do not deliver in the expected product quality, you will not be able to keep your new customers. The use of our scanners helps to maintain quality.
2. Do you have a high fluctuation of staff?
The plant manager looks at the quantities, the quality manager at the required quality level. Without a reliable evaluation system of which product quality is acceptable for which customer, staff at the visual inspection station easily get caught between two masters with diverging objectives. The result is dissatisfaction with the operation. Staff need defined procedures and a clear specification of what is to be assessed as "good" or "bad". A scanner is the objective basis for setting quality levels for individual customers or the company standard. These determinations should be made in cooperation between the operations manager and the quality manager.
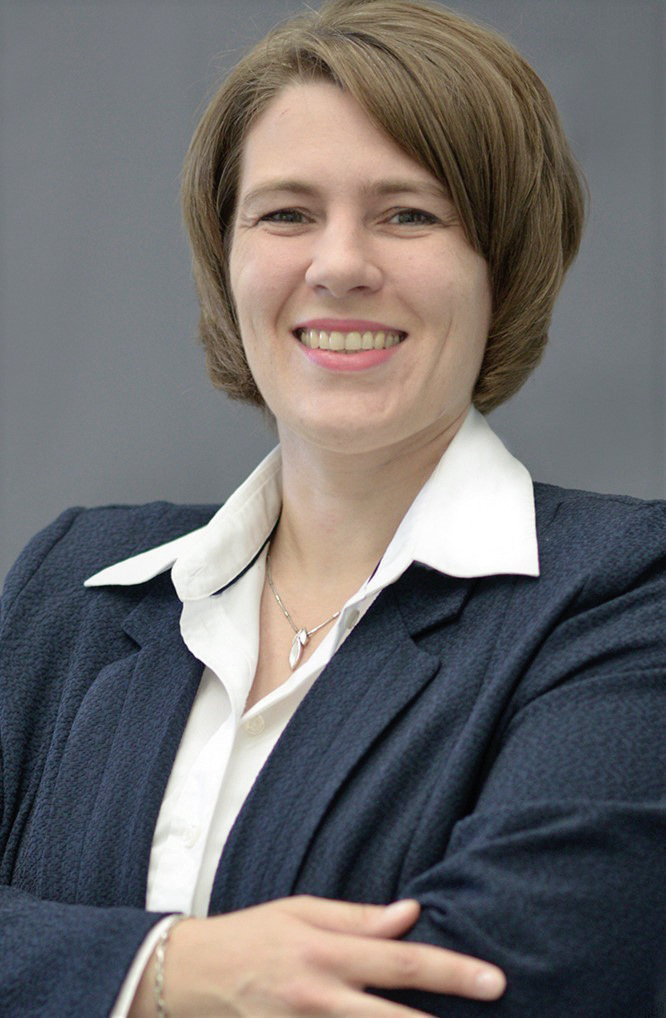
Viprotron
3. What does automation have to do with scanners?
The new possibilities for automation in various areas of production and the trend towards IoT/Industry 4.0, "umati" or "OPCUA" are bringing new momentum to the linking of operational steps. The more closely these steps are linked, the less people have access to the glass product. Cutting staff for cost reasons is a desired effect of automation. Nevertheless, if there are no production staff, there is no one to keep an eye on product quality. Complaints are almost inevitable. Can this be what you want?
Also interesting: New partnership in tempered safety glass quality inspection
Viprotron scanners can provide a remedy here and be used at various points in production to avoid just this. With up to three channels and a defect classification based on these, quality control is then carried out, which is also possible in the context of automation. For example, the Quality Scanner 3D can distinguish between water drops and bubbles in the glass, because you don't want to stop your lines because of water drops.
4. How to plan the expansion of the factory equipment?
You are planning a new location and ask different suppliers for their quotes and layouts. This often leads to planning through new sites without including the issue of quality control.
If at all, this aspect often only comes into play "five to twelve" - and then work processes and thus layouts have to be rescheduled. But by this time, the machinery for the cutting area has often already been ordered, the clean room for the LSG can no longer be changed or the insulating glass line has been incorrectly configured for reasonable quality control. Viprotron is happy to help with the design of the desired inspection equipment, which helps to avoid expensive conversions later on.
5. Are your reclamation costs going up?
Many companies often have only a vague idea about their reclamation costs. Some only see it in the glass containers with customer returns. Others try to find out the reasons for complaints manually and thus cost-intensively.
See also: Flachglas Switzerland: Quality is a key to success
If the processor uses one or more scanners, it gets an overview of problem areas in production long before the product is on its way to the customer. In this way, scanners not only help to avoid unnecessary stress in production, but also third-party costs (including special transports, scaffolding/crane costs, reglazing).
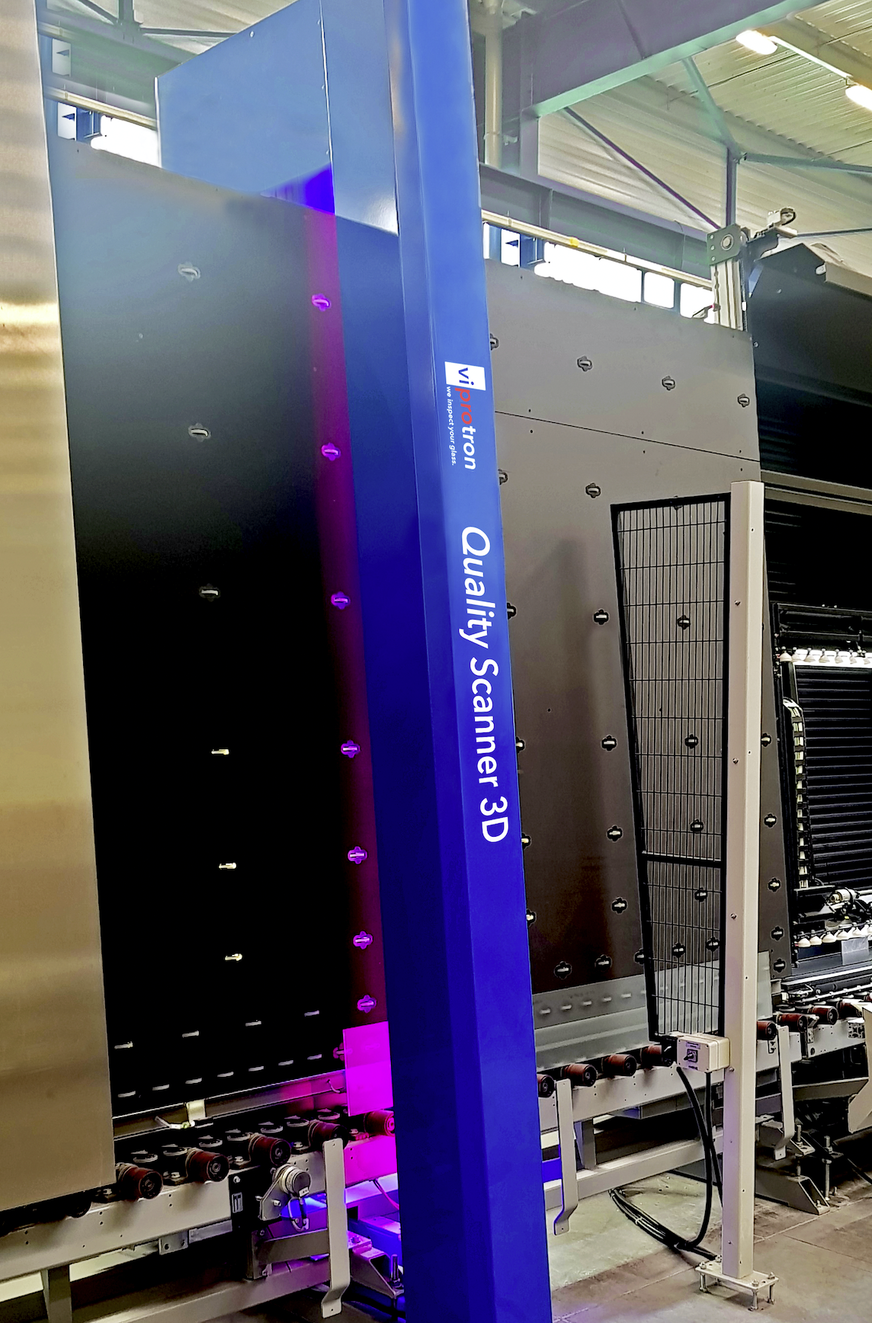
Viprotron
6. How can products be "tracked" through the production process?
Do you already feel that the obligations to provide proof and the necessary documentation are a major bureaucratic act? And now the customer is also asking you to "track" product quality? Viprotron scanners can help here, because the inspection results as well as the other data generated by the scanner itself or read in before the scanning process can be assigned to the respective glass pane with a time stamp etc. and stored in any location on the customer's server. This data is thus available for ERP or PPS packages and supports efforts to track the glass and its components very precisely throughout production.
7. Is your manufacturing environmentally friendly?
Glass consumes a lot of energy in its production, we should not waste it, not only because of the cost. Viprotron scanners can reduce scrap rates because they can find defects before they are cut or during the production process. If defects are found before the final product is finished, the glass can often be cleaned or reworked. This does not only apply to the glass. In this way, all materials that are processed later, such as interlayers or spacers, can be salvaged. If defects are only found in the finished product, unnecessary transport of the glass panes can at least be avoided.
Did you miss this? Full quality control in flat glass production
8. Do you want to sleep easier?
The following should be a familiar situation to many: You come in to work in the morning and during the late or night shift, dozens of glass panes or even the entire shift's output had to be scrapped due to a series defect. The fault was found too late and now not only are additional costs looming, but production also has to make up for the shortfall. And this with an already very full production schedule. Viprotron scanners will allow you to sleep easier again. The right scanners used correctly help to avoid unnecessary stress. What could be better?