Upon closer inspection, there are plenty reasons to fault awning installations, issues which would have to be highlighted in inspection reports. This issue is often the subject of heated debate. The companies responsible for installing the awnings usually argue that, “awnings stay up anyway and there’s no need to comply with all the rules and regulations”. But is that really the case?
Let’s have a closer look. The sector did of course install awnings before 2006 – at that time plastic dowels were the fixings used. Sticking was also used then, but only in manageable doses, primarily due to the significant price difference. A plastic dowel for a few cents was deemed significantly superior to a single injection anchor for 10 euros and considerably greater installation time, at least from a business perspective. And the awnings are still hanging today. So why all this? Are the regulations, standards and guidelines really justified? Is the extra effort really worth it?
The answer, when it comes to safety, is yes, absolutely.
Let’s take a few examples from the automotive industry. It’s amazing how many things can be explained clearly using cars and driving as an example. Twenty years ago, a rural road had a speed limit of 60, a decades-old practice for car drivers until, suddenly, out of the blue, a nursery was built on the street. A few braking manoeuvres later and, all of a sudden, under pressure from worried parents, the lovely street is plastered with 30-kilometre signs. This is more or less a similar, in a figurative sense, to what happened in the awnings sector after the DIN EN 13561 “Awning standard” was introduced in 2005 with a transitional period of a year. There was substantial moaning and groaning in the sector but fortunately most installation companies comply with the newly prescribed “speed limit” and blinds manufacturers deliver the corresponding calculation tools, i.e. a fully legitimate version of a speed camera warning device, free of charge. So what’s the problem?
Just like road traffic, every accident, regardless of its consequences, is one too many. The problem here is those installation companies equivalent in our comparison to speeders in front of the nursery, who install awnings incorrectly, without consideration for the regulations and guidelines in force.
The consequences? In most cases none, because there are no “speed traps” so to speak. It’s not until there’s a storm and the awning is extended and comes down in the rain or the awning is examined by an expert for paint scratches that anyone takes a closer look. And then, all of a sudden, it's there for all to see, obviously faulty assemblies which, upon closer inspection, pose a safety risk and may be penalised. Not with points in Flensburg, but with a repeat installation or a substitute performance by a third party. The estimated number of unreported cases? Without verification it’s not possible to make any definite assertions. The same applies to the nursery, the only thing that can filter out the speeders is speed guns.
The problem area of edge and hole spacings
But there are two sides to every coin, and it would be unfair to place all fitting companies under general suspicion. Just like road traffic, there are tolerances. For instance, somebody driving past the nursery at 34 km/h will not be penalised. 100% perfect assembly isn't always possible.
The issue of edge and hole distances is particularly problematic. And it’s often here that fitting companies walk right into a trap because they simply install the awning brackets supplied by the manufacturer with fasteners approved by the relevant building authorities (ETA approval) and think themselves safe. But are they really safe? Of course not, because ETA approvals are subject to conditions that have to be complied with. That is why good awning manufacturers provide their customers with technical documents which explain which bracket should be fixed on which base. Digital bracket planners are currently regarded as the ultimate solution for certainty. The only problem? You have to use them. Saying, “we’ve been doing this like that for 20 years” is little use here, because now there’s a 30 km sign there and anyone who doesn’t see it will quickly get a ticket.
If we look at the picture on the left, it’s clear that the issue of edge and hole distances is a home-grown issue too, because the building heights of the awnings and their design specify the height of the hole distances. Awning manufacturers could create better framework conditions by supplying wider brackets with greater hole distances as standard. What might work well in the example on the image on the left where the awning has been installed on concrete will not work on perforated brick. Many manufacturers offer wide brackets as an added extra for a fee, but these are not used by fitting companies in most cases on account of the high costs.
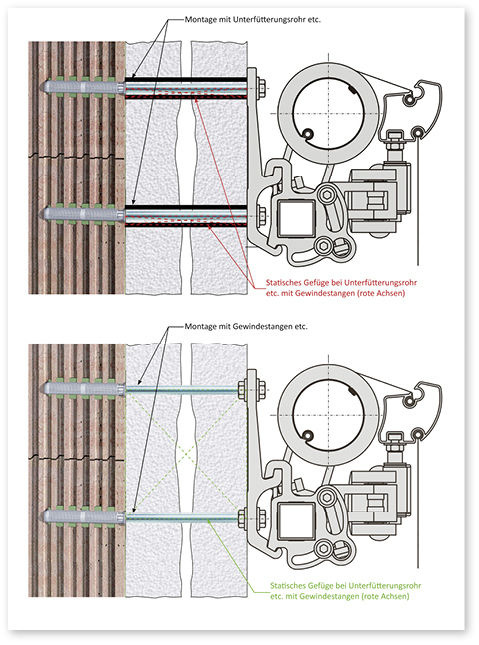
ETA approval
ETA approval is not about using a fastening which has ETA approval but complying with the specific framework conditions applicable to the installation. Reading is obligatory when it comes to fixings with ETA approval. This is the only way to ensure secure installation in the relevant fitting circumstances and given the requirements profile. That is why each ETA stipulates that the use of the fixing must be overseen by a foreman, engineer etc. This specification should be taken seriously, especially given the fact that foreign-language employees often cannot understand the specifications of an ETA due to a lack of language skills.
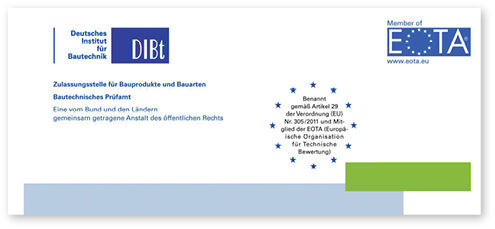
Conclusion
If you follow the program sequence for selecting the fixing (see left) and the relevant manufacturers’ specifications, you can’t go wrong. It can all be so simple if you have the relevant knowledge. As the saying goes, “once learnt, never forgotten”. Another reason for reintroducing the master craftsman certificate in the roller blind and sun protection trade.
Author: Olaf Vögele