The company, founded by Fortunato Vianello, is proud to be one of the first glass machine suppliers to have developed a complete vertical glass processing line. When he founded Forel together with his brother Elio in 1976, the aim was already to implement glass processing and the production of insulating glass completely vertically in order to facilitate production for processors.
In addition to the insulating glass lines, Forel also offers vertical processing centres and cutting systems for laminated glass, as well as machines for edge processing and polishing.
See also: Offering a variety of insulating glass products for northern Italy
Carlo Zuccarello, Forel's Sales Manager, explains: ‘Vertical lines have two major advantages: firstly, vertical machines require less space in the workshop and thus allow more flexibility, including in the layout of the line. This is particularly important for existing production halls with limited space. Secondly, fewer components are required to move the glass from a horizontal to a vertical position.’
Laminated glass up to 1.5 tonnes
And Zuccarello continues: ‘Every Forel system is customised and meets the specific requirements of the respective customer. And that is exactly what our customers appreciate very much.’ Our systems are modular and can be put together from a wide range of components: cutting and sorting machines for laminated glass up to 6 × 3.3 m, as well as solutions for internal logistics and glass processing, and, of course, insulating glass lines.
For example, a complete line for the production of laminated glass was recently developed, consisting of a washing machine, a magazine for various PVB films (which are automatically selected and positioned), a heating and pressing station, and a tilting table for glass panes weighing up to 1.5 tonnes.
What the vertical IGU lines can do
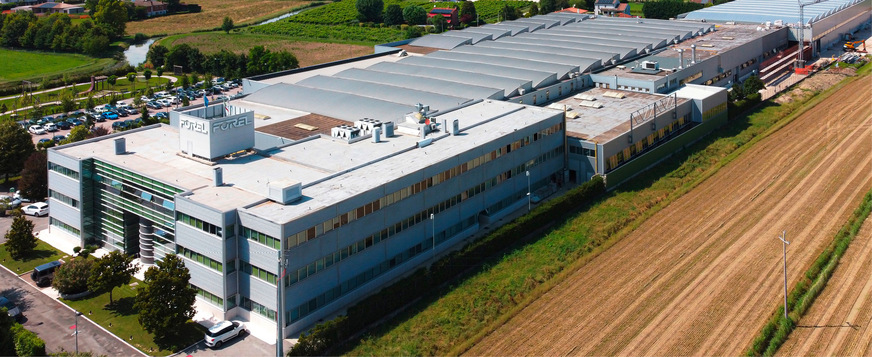
Forel
Forel currently offers a range of systems for insulating glass production, from the Essential Line for insulating glass up to 200 kg to the No Limits Line for insulating glass formats up to 9 × 3.3 m and weights up to 550/m kg. All Forel IGU lines are compatible with the three common types of spacer bar, i.e. with rigid, with flexible and with thermoplastic spacers.
Sales Manager Zuccarello: ‘The modular line design makes it possible to adapt the lines to growing capacities.’
The entire production process, from construction to installation and quality control, takes place in northern Italy.
Multilingual helpdesk
The worldwide distribution of the plants requires comprehensive service. Forel offers a free, multilingual helpdesk that connects customers directly with the responsible technician for troubleshooting. Virtually all Forel machine modules have a dial-in function for error analysis by the service technician.
The sales manager explains: ‘The plants must not fail unexpectedly, and certainly not in highly automated and networked production environments. If it does happen, however, it must be possible to get the system back up and running immediately. Our helpdesk is on hand to provide support. From there, our service technicians can intervene immediately and connect to any Forel system remotely. This usually allows us to solve problems immediately and get the system back up and running. In all other cases, we send a service technician to the customer as quickly as possible."
Innovation is key
Over the years, Forel has not only steadily expanded its product range, but is constantly exploring new business opportunities, such as plants for processing thin glass.
This type of glass is required for applications where weight is an important factor. Forel's innovation team is currently working on the implementation of an automated production line for thin triple insulating glass units.
High employee satisfaction
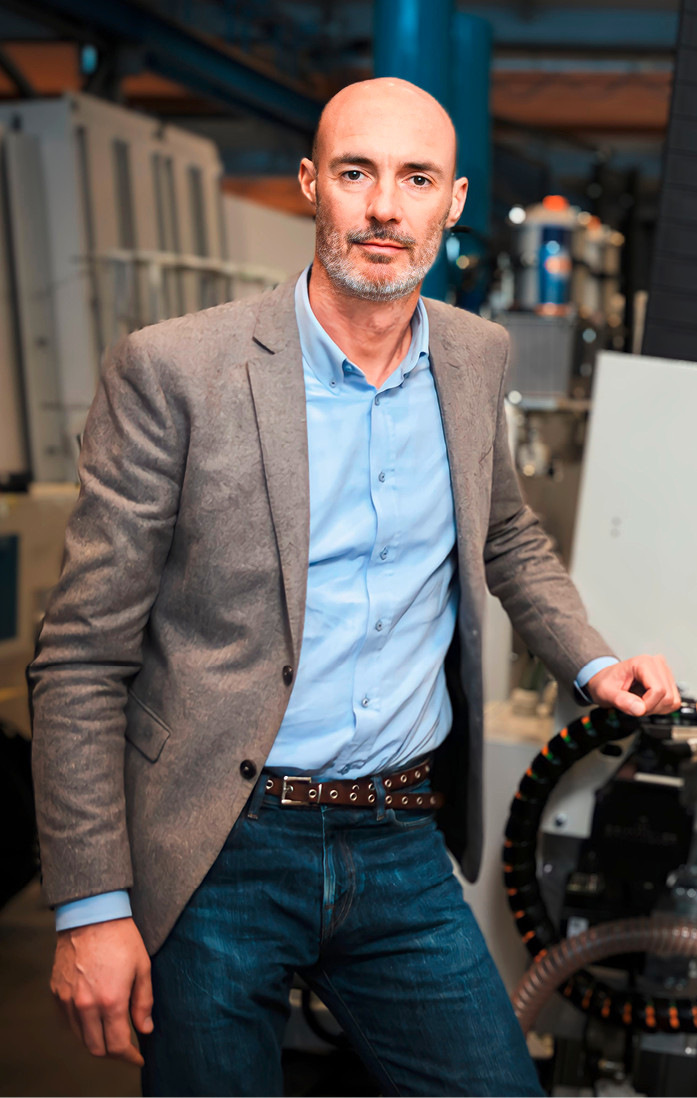
Forel
Happy employees are an important factor in success. With this in mind, Forel offers a wide range of facilities at Roncarde that employees can use free of charge, including sports, fitness and gymnastics studios, weekly physiotherapy, a canteen and summer camps for children.
Carlo Zuccarello: ‘We want our employees to feel comfortable at work. This not only motivates them at work, but also strengthens employee loyalty due to the family atmosphere we create. With all these offers, we also want to show our employees the appreciation we have for them, because good employees are ultimately the basis of our success.’
Growth and future plans
In addition to its headquarters in Italy, Forel also has subsidiaries in the UK, the US, Canada and South Africa. Carlo Zuccarello: ‘We are well positioned. In addition to our founder Fortunato Vianello, his son Riccardo has also been active as CEO of the company for many years, thus ensuring succession. Furthermore, we have a global network of over 30 partners who install and maintain Forel systems in over 70 countries.’
Also interesting: Fenzi Group acquires Thermoseal and enhances IG product range
Forel has ambitious plans for the next few years and is focusing on sustainable growth. In addition to strengthening its position as an international player, the company plans to further expand its presence in EU markets and in the German-speaking region of Europe. ‘The German market represents an important opportunity for us,’ says Sales Manager Zuccarello. ‘And we are working hard to expand our position there. That is why we will also be represented at glasstec 2024 with a large stand (1200 m²)."
Carlo Zuccarello: “As we want to grow, we are currently expanding our production. Part of this is a new hall (9000 m²) in Roncade, which will enable us to adapt our capacities to meet the increasing demand.”
Malte Forstat