For special construction and facade projects, architects are increasingly looking for facade glazing that is customised to suit the project’s specific demands. With its Coating on Demand service (CoD), Interpane is now able to give them what they need. The service enables the company to provide glazing that is fabricated independently of the standard product range.
The “core” of this service is the rendering software that is able to simulate the coated glass in realistic installation scenarios in true colour. All physical properties and the climatic conditions at the site are taken into account.
Gregor Ranner, managing director of Interpane Plattling: “Architects can use the rendering software developed by AGC Glass Europe to experiment, as it can simulate the coated facade glazing in realistic lighting conditions and installation scenarios. It also takes into account all the coating combinations we are able to produce and our entire glazing range.”
What planners see is what they get
The CoD rendering software makes it possible for clients and planners to experiment and play with light transmission, reflection and the aesthetics of coatings so they can find the perfect configuration for their particular project.
Once all technical and visual properties have been defined, the program performs a feasibility check and optimises the configuration as necessary. Once the defined parameters have been determined, initial glazing samples are created directly at the Interpane plant in Plattling and are available for viewing just one day later.
Along with the customised coating, Coating on Demand offers maximum time savings – an advantage that the supplier highlights – as a new product can be defined in just one day. In the end, the architect/client receives a product that is unique, as AGC Interpane will not use this configuration for any other building in the world.
The first projects to make use of CoD were the Hotel VIU in Milan and the Vista Tower in Chicago. For the latter, the architects wanted to integrate a “colour gradient” into the facade. This gradient is made up of six differently coated glazings and covers the entire glass shell of the multi-storey building.
This wasn’t all that easy, according to Gregor Ranner: “Firstly, there needed to be a significant colour difference from one type to the next, if the desired effect was to be achieved. Secondly, the difference in colour could not be too extreme, as this would give the facade a chequerboard appearance. This is where we were able to impress with our rendering software, even in the planning stage. With this and the corresponding Coating on Demand service, we were ultimately awarded the project in Chicago.”
With the CoD service, the company offers the advantage of maximum time savings, along with the customised coatings. “With our property centre in Plattling, we only need a day to define a new coating product. This is only possible because our site has both high-end coating and its own insulating glass production facilities, where the test panes are fabricated,” Ranner continued.
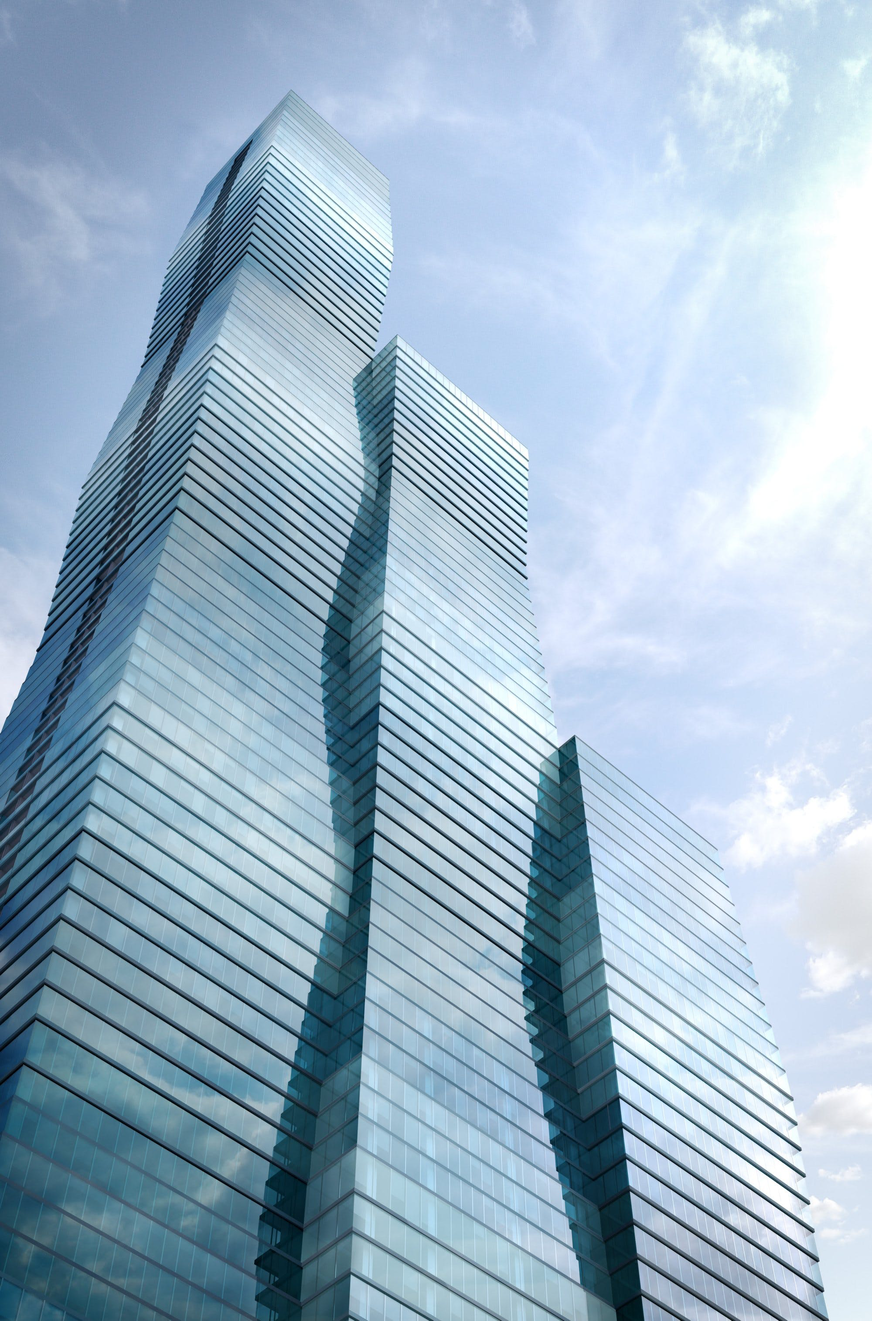
Glazing reproducible at any time
However, the supplier (www.interpane.com) not only supplies products but also provides consulting for planners and clients in matters relating to the project progress and scheduling. As Ranner explains, “We have lots of experience in handling major international projects, and this helps the customers.”
But what would happen in one of these custom-made panes, or specifically panes with customised colours, ends up breaking at the construction site or on the way there?
Even a breakage would not faze the glazing specialists from Plattling. As Ranner says: “As the parameters for the particular coating, or coating colours, are saved in our digital archive, all panes can be reproduced later on if a pane ever needs to be replaced. There is no need for planners or owners to worry, as this is something we have already made provisions for.”