What role does microplastic play in glass transport? When flat glass sheets are transported from the float glass plant to the glass processing plant, adhesive forces and chemical reactions can cause a solid bridge to form between the glass sheets, making it difficult or actually impossible to separate them later.
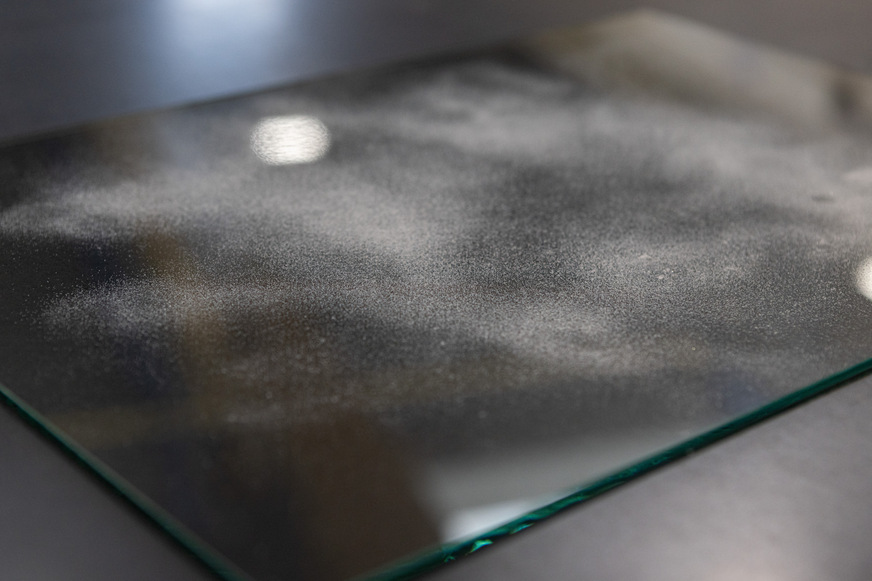
Lisec
Historically, this problem was solved with interlayer paper. Today, more cost-effective interlayer powders are used, which also prevent scratching of the raw glass panes. Conventional glass release agents consist largely of microplastics, i.e. plastic particles smaller than 5 mm.
How does the glass release powder make its way through production?
Every year, several tonnes of glass release agent are used per float glass plant worldwide. The release agent is delivered with the glass panes.
See also: Euroglas shifts to environmentally friendly release agent
After the glass storage system (e.g. from Lisec) has separated the individual glass storage plates, a large proportion of the release agent is removed with a static or rotating brush. After the glass sheets have been cut to size on the cutting table, the remaining glass release agent is washed off.
In the worst case, the residues of the glass release agent end up in the waste water and thus in the environment, where the plastic particles remain for centuries and are broken down into ever smaller particles.
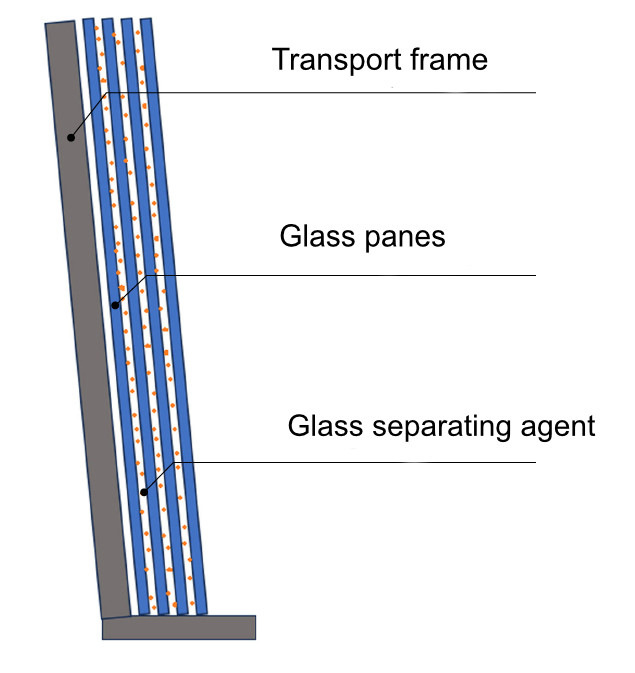
Lisec
What microplastic-free alternatives are there?
In order to protect the environment and comply with the new regulation, manufacturers and importers of glass products must ensure that no microplastics are released into the environment or that they use alternative release agents that are biodegradable.
Also interesting: Minimised carbon footprint - Saint-Gobain and Hydro join forces
Leading release agent manufacturers have therefore been researching plastic-free alternatives to conventional interlayer powders for some time.
The new materials have been tested for months. They are based on a natural, renewable raw material, can be both processed and removed using the equipment available on the market and so far no negative effects on the quality or processing of the glass have been identified.
Author: Sarah Hummelsberger, Production Assistant at Lisec