The new sorting concept simplifies the introduction and re-production of missing or damaged units. In addition, the previous strict dependency between dispatch and production is eliminated. This puts the previous production principle to the test and opens up additional optimisation possibilities: The dispatch sequence no longer dominates IGU production.
See also: Hegla re-invents insulating glass recycling
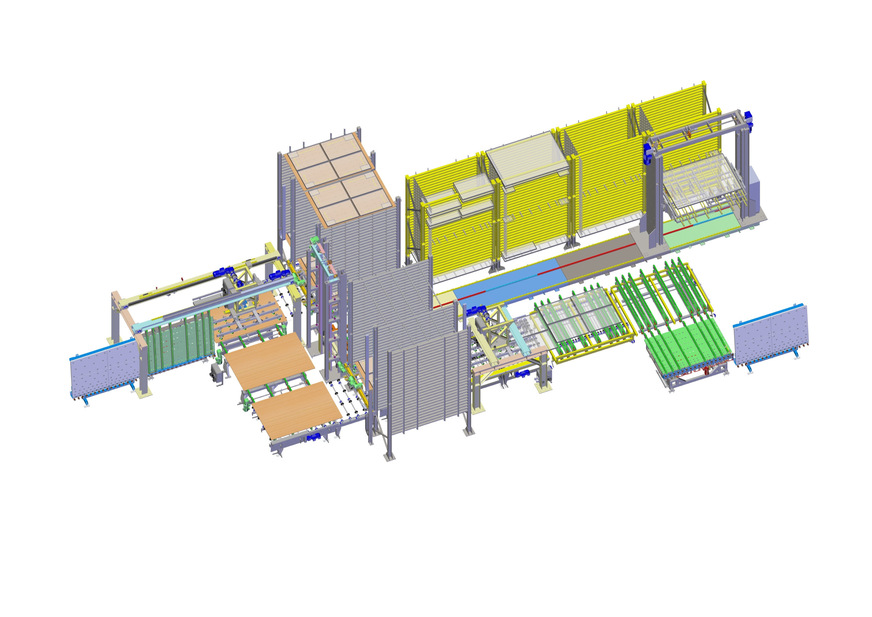
Hegla
As a rule, the order batch is organised in descending order from large to small formats so that the units can be transferred to A or L racks in the dispatch sequence without restacking. If re-production is required, for example due to scratches in the glass, this sometimes leads to the shipping process being interrupted and the glass racks having to be placed in another area of the hall, which is time-consuming and labour-intensive. Alternatively, the post-produced units are placed on additional racks so that the desired sequence has to be manually restored later by the employees.
Combined drying and sorting racks for finished insulating glass units
By buffering the insulating glass units produced, the new SortJet IG sorting system decouples the processes between production and dispatch, reducing direct dependency: Loading of the racks only begins when all units of an order have been produced. For this purpose, up to four insulating glass units are automatically transferred to a transition plate immediately after completion on the line and stored in a drying tower. Depending on the configuration, they are removed after curing and transferred to a horizontal sorting store.
Also interesting: That was glasstec 2024 – a trade fair retrospective
Once a customer batch is complete and ready for dispatch, the operator or the software triggers the staging process and all glass panes are output in the required sequence. Finally, intermediate storage and optimised merging enable reliable glass transfer in sequence, which makes it possible to use robots as a further expansion step to reduce the workload on personnel.
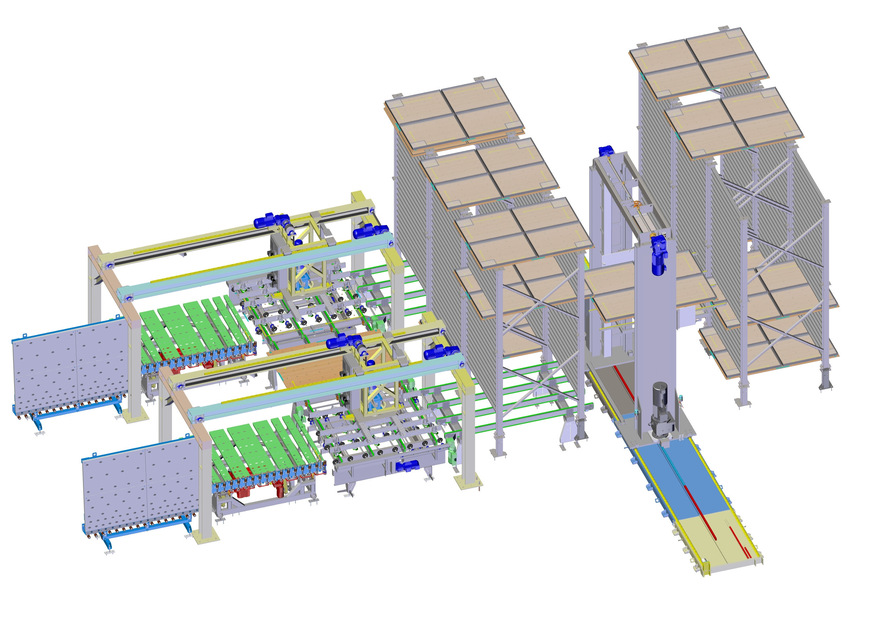
Hegla
Further optimisation potential
As soon as the production requirements between the insulating glass line and the shipping provision are relaxed, further optimisation potential arises. Depending on the customised equipment of the insulating glass line, it is advantageous in terms of set-up times, for example, to produce single-variety double or triple glazing.
In addition, batches with the same gas filling or the same sealing material can also lead to improved processing times.
This system was a real visitor magnet at the trade fair.