“The future will remain challenging, dynamic and anything but boring,” says Hegla Managing Director Bernhard Hötger. “New products and applications, changing legal conditions, higher cost pressure, the shortage of skilled workers and the looming crisis in the construction industry will all have an impact in the foreseeable future,” he added.
Shop-floor logistics as cycle-based material provision
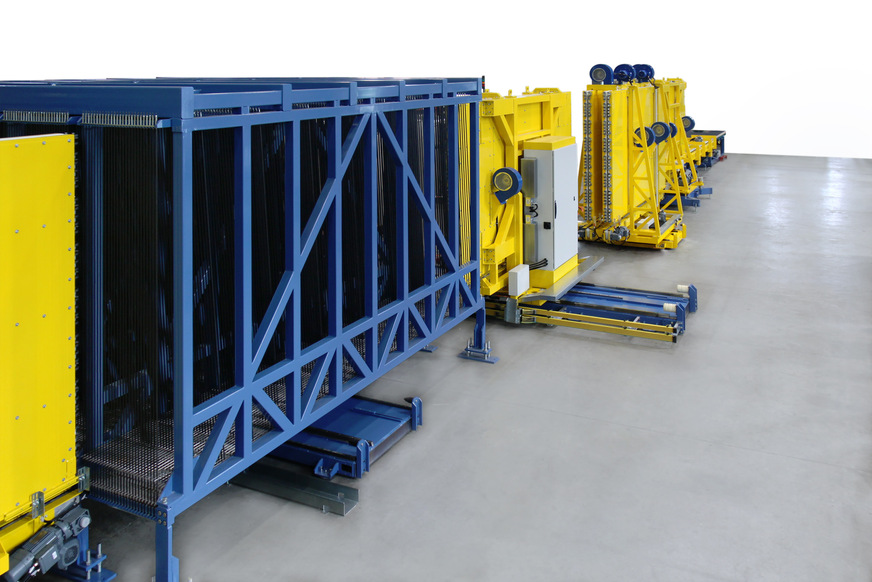
Hegla
“A batch size of one has always been an essential core of the glass industry, which is why it is the focus of any vision of the future,” said Hegla Managing Director Bernhard Hötger. Many aspects of Industry 4.0, like stringent production requirements for non-serial products or the aim of networked production, are already part of the daily routine in the industry and have reached a new level with every technological advance.
This makes the continuous optimisation of shop-floor logistics a consistent approach that will become an even greater focus: How can the material flow be managed to enable continuous production at all processing stations? How can the potential of the systems be fully tapped? “As a trend, automation, digitalisation and user-friendly processes are familiar faces that we have been working to implement for years,” explained Bernhard Hötger. “The performance of European quality machines is so high that the productivity of the system is not the single deciding factor. Their integration into the overall process and needs-based material provision are just as important. Perfectly coordinated processes increase the system’s productivity, reduce effort and improve quality. On the one hand, this sustainably reduces unit costs and, on the other hand, the processing stations are utilised better for higher competitiveness.
Fit for the future
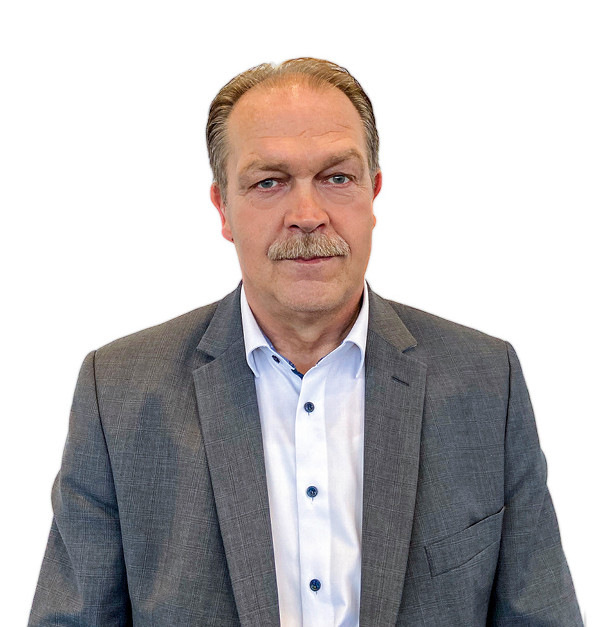
Matthias Rehberger / GW
In searching for the right point of departure, it is important to look at the overall concept and the value stream: How are orders recorded and information passed on? Which production steps are directly dependent on each other and what material flow is needed? Which activities can be digitalised or automated in order to increase productivity, reduce the error rate and support skilled workers even better in the value stream cycle?
“Be it digitalisation, software or system solutions, individual companies have widely varying options for optimisation and different needs,” said Bernhard Hötger. He advises companies to conduct integrated value stream analyses that include the shop floor with its material dynamics and software, to identify the sum of their potential.
Based on experience, in the first step, they should look at the processes by which the glass is manually provided or transported, how data are maintained outside the system and when manual handling is necessary. In one case, an automatic X-/Y-breakout system that automates the manual breakout process and lightens the operator workload promises advantages.
In another case, laser marking that replaces label application and gives the glass a unique identity that can be tracked via scan for production management and product traceability is the most beneficial approach. A sorting system with online glass transfer can provide advantages, as can automated removal from harp racks or the ReMaster remnant handling system.
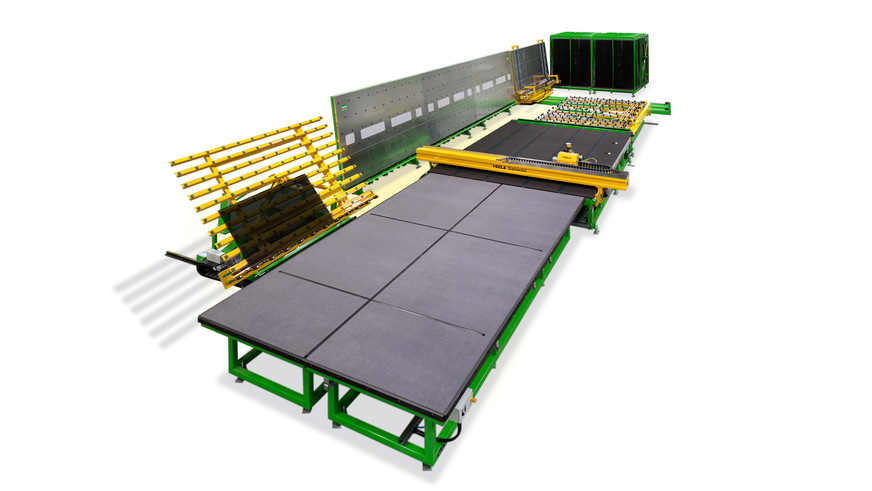
Hegla
Without interrupting the cycle time, the resource-saving ReMaster retains usable leftover glass above the cutting line until it can be optimally used for further cutting. Operators can focus on the productive cutting process and are no longer involved in removing, putting down, positioning or searching for panes – ensuring a continuous glass flow to the downstream processes.
Flexibility: Combination systems are back
A close look at the trend for more automation shows the outlines of another development. Demand for combination cutting systems for float glass and LSG has risen significantly and the systems are more frequently paired with breakout stations. Combination solutions lightens operator workloads, improves cycle times, standardises sequences – and a further reason for their renaissance is increased flexibility. Further, if extra capacity for peaks in the float glass or LSG areas is required, they can provide it. The more completely the glass flow is linked up and embedded between the processes, the more reliable the overall workflow.
Software: Dynamic continuous optimisation
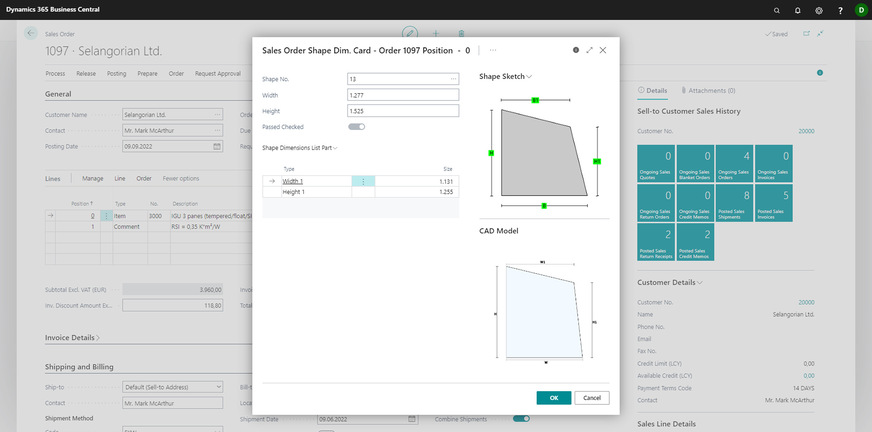
Hegla
At Hegla, no employee area has grown as rapidly as software development in the past 30 years. This is an indication of the profound changes that have taken place in machine manufacturing and the glass-processing industry. The importance of software will continue to rise and will become an essential component of an integrated reference system, at the latest when it comes to the concept of shop-floor logistics.
See also: Hegla boraident: The laser as "bird protector"
The more thoroughly processes are combined, the easier it is to maintain an overview and optimise sequences. “This is why we advise other companies to look for potential at the places where their data exits the system or is transferred by operators,” explained Bernhard Hötger. “If ERP, capacity planning, optimisation software, BDE and MES are fully networked, data analysis can be more meaningful and highlight gaps or breaks in glass provision and in the processing steps.” Continuous tracking of the markings on the glass yields more knowledge about the glass flow, dependencies and cycle progress.
Alongside the major area of automation, software optimisation is a second key future theme and is the focus at Hegla-Hanic. When it comes to classic cut optimisation, the experts there recommend an enhanced form of dynamic continuous optimisation. For incoming new orders or rush jobs, the cutting plans are adjusted in real time and, depending on the configuration, can refer to several batches so that waste can be additionally reduced.
Optimisation across the entire shop floor according to the dynamic pull principle is even more far-reaching. By tracking the entire production flow or pieces of it across all areas, workflows are comprehensively monitored and, if a delay is flagged on an insulated glass line or urgent orders experience delays, for example, production can be adjusted in real time. This function can also be practical when a processing station fails: the glass flow can be re-optimised accordingly to ensure that the glass flow to downstream processes is maintained.
Employees take centre stage
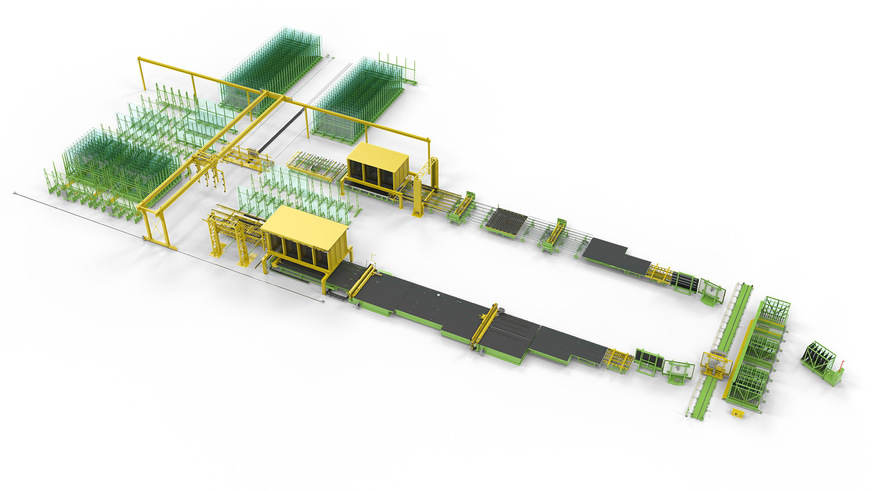
Hegla
“In its long history, the glass industry has always been a manual trade and will continue to be carried by people and their know-how in future,” stated the Hegla Managing Director. To increase productivity and show appreciation for employees more clearly, the focus will also turn to support for the people on the shop floor. The mission will be to make activities even more user friendly and provide exactly the information required to do the job and make informed decisions.
“With cockpits, dynamic optimisation, practical guidance and the right handling equipment, we can improve the workflow and assign skilled workers to the activities that require their qualifications and skill set.” The labour market will feel the effects of demographics more acutely in the coming years and, with the increasing complexity and variety of glass products, it will be even more important to give employees structure and assistance.
The overall system must fit together, and the cycle of the value stream of information, material and productive human working hours must be equal and balanced in order to ensure a continuous production process. As soon as machine performance, the material flow and the human factor optimally mesh and are mutually guided, productivity is ensured and the risk of imbalance caused by downtime or delays is systematically reduced.
Legal framework and climate change as an opportunity
“While the markets are reporting an initial downswing due to the current construction industry crisis, the financial and legal pressure to renovate presents an opportunity,” said Hegla Managing Director Bernhard Hötger. During the winter, the price of energy will probably rise again, boosting the incentive for property owners to invest more in existing buildings and the building envelopes. Further, new funding programmes that provide economic stimulus for renovation can be expected, and their impact will be reinforced by new energy efficiency laws.
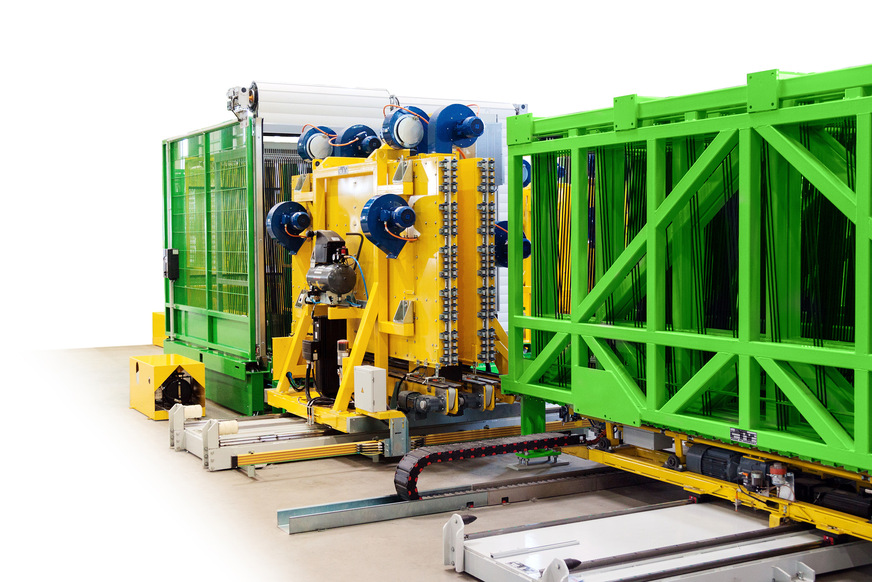
Hegla
“The market for special-purpose glass has a positive trend. Demand for both bird protection glass and RF-transparent glass is higher than ever,” added Bernhard Hötger. Finishing treatments that turn standard panes into products with added value offer an opportunity now to circumvent cost and competitive pressure.
Also interesting: 5 answers on electric mobility for tradesmen
“Cost savings and improved productivity have always been a continuous development process in the history of the glass processing industry – but their actual implementation has become a more significant success factor than ever before,” explained the Managing Director. Once the overall process has been optimised, potential that provides economic security can emerge. Bernhard Hötger is convinced: “At some point, we will have weathered the next crisis as well, and the companies that are perfectly positioned will reap multiple benefits.”
The shop-floor logistics approach involves automation and digitalisation and targets a workflow in which the full potential of the systems is consistently achieved through needs-based materials provision.
A sorting system with an online connection enables cycle-based glass transfer to downstream processes without manual handling. Interim buffering of the panes in the dynamic SortJet storage system additionally optimises waste and enables processes to be flexibly managed.