The construction industry in the US is looking to 2024 with confidence. Sustainability, energy efficiency, durability and comprehensive government subsidies are key drivers. This offers attractive prospects for European manufacturers in particular, as construction products from Europe enjoy an excellent reputation for quality. Swisspacer has responded to the current development by opening a distribution centre in New Jersey in the immediate vicinity of New York.
See also: What do Americans think about windows Made in Germany?
High inflation, increased raw material prices and a shortage of skilled labour initially resulted in only moderate growth in the construction sector in the United States last year. However, several billion-euro government subsidy programmes and tax incentives could lead to the construction industry gaining significant momentum in 2024. "The construction industry in the US is undergoing a remarkable transformation, driven by technological advances and a growing focus on sustainability," says Matthias Bach, Managing Director of warm edge manufacturer Swisspacer.
Rethinking in the US offers opportunities for Europe
Energy efficiency in particular is likely to become a key factor for sustainable construction. The corresponding upfront costs can be offset by lower long-term life cycle costs. Cost reductions can be achieved, for example, through the use of high-performance facades and energy-efficient systems. "We see that energy-efficient and sustainable buildings are becoming an important part of the American construction industry. In individual states, the trend towards zero-net-energy building codes is increasing. At the same time, building certifications such as LEED and BREEAM will continue to grow in importance," Matthias Bach is convinced. "Interest in and commitment to environmentally friendly building materials and products is growing noticeably. This also offers a great opportunity for European manufacturers of building products and materials and materials to benefit from the current trend".
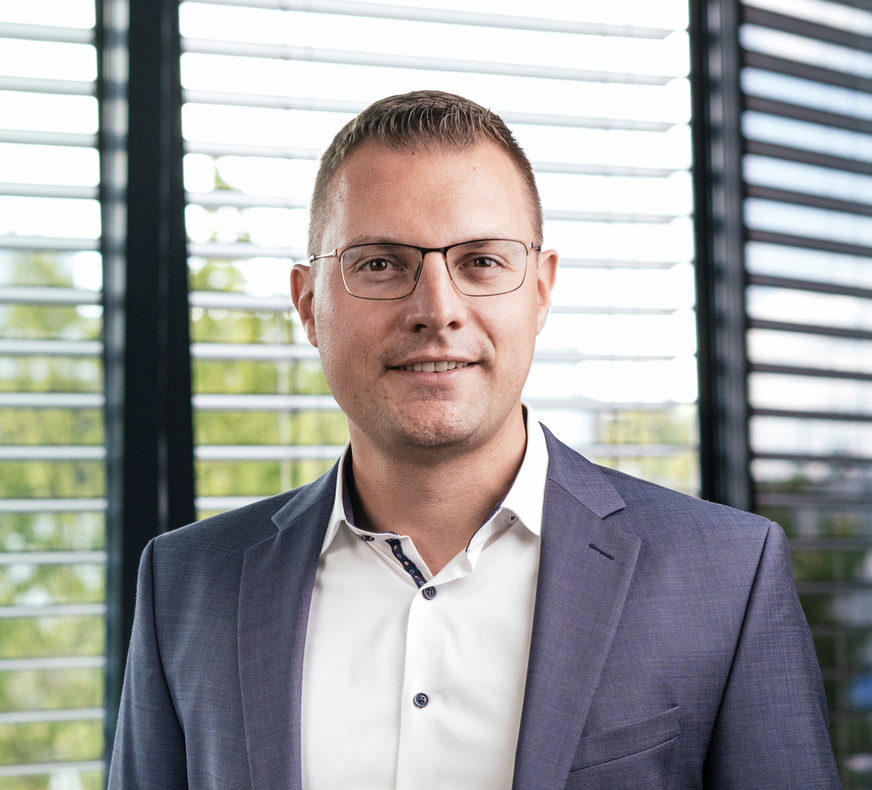
Swisspacer
It is important to familiarise yourself with the local building codes. For example, the highest requirements for windows apply in the north-east of the US and in California. "The sizes and designs of window and door elements also differ from our European standards," explains Matthias Bach. For example, small-format vertical sliding windows are usually found in private residential construction - and not the tilt and turn windows that are common here.
On-site warehouse for short delivery times
Economic uncertainties such as raw material prices, energy costs and material availability are also affecting the American construction industry. "Local companies will adapt their business processes," Matthias Bach is convinced. "They will make more agile decisions and continuously optimise project and procurement processes. That's why we decided to set up our own warehouse on site. This means we are close to the market and our customers and can also respond to very short-term requirements. In addition to quality, product portfolio, aesthetics and sustainability, security of supply is also a key factor in gaining a foothold in the American market," explains Swisspacer Managing Director Matthias Bach.
Also interesting: Elmar Rastner now in charge of Swisspacer for Europe
Swisspacer's warehouse is located in Closter, New Jersey, near New York City. The Ultimate Pro, Ultimate, Advance and Vienna Spacers will be available locally, customised to local requirements. The warehouse is the first distribution centre for spacers from Swisspacer products in North America, with the first deliveries of spacers taking place in April. "With the distribution centre, we are not only making our products available for the American market, but also want to establish ourselves locally as a competent partner for the production of the most energy-efficient windows and facades," emphasises Matthias Bach.