The T-Rail is an innovative side seam component that is attached to the textile edge using an ultrasonic bonding machine. It consists of a flexible fabric and a dimensionally stable inlet, which are combined to form a foldable ‘T’. This offers two main advantages over the current ZIP solution: when rolled up on the fabric shaft, the T-Rail is as flat as the textile itself, as the ‘T’ folds down and lies next to the textile. Tests during the development phase have shown that TRail can withstand more than 40,000 cycles, significantly exceeding the 10,000 cycles required by DIN EN 13561 in accordance with service life class 3.
See also: An awning system for outside seating in any weather
If the textile is traditionally wound with a side zip, the result is uneven winding. The zip is compressed while the fabric lies flat on the shaft. With each turn, the differences between the fabric and the zip are doubled. Manufacturers therefore try to create more space for the zip by lowering the fabric shaft. However, this is only possible to a limited extent with smaller shaft diameters. The different winding diameters on the ZIP to the textile on the fabric shaft can lead to overstretching, which is characterised by the formation of creases in the edge area. In addition, the ZIP system requires a minimum box size.
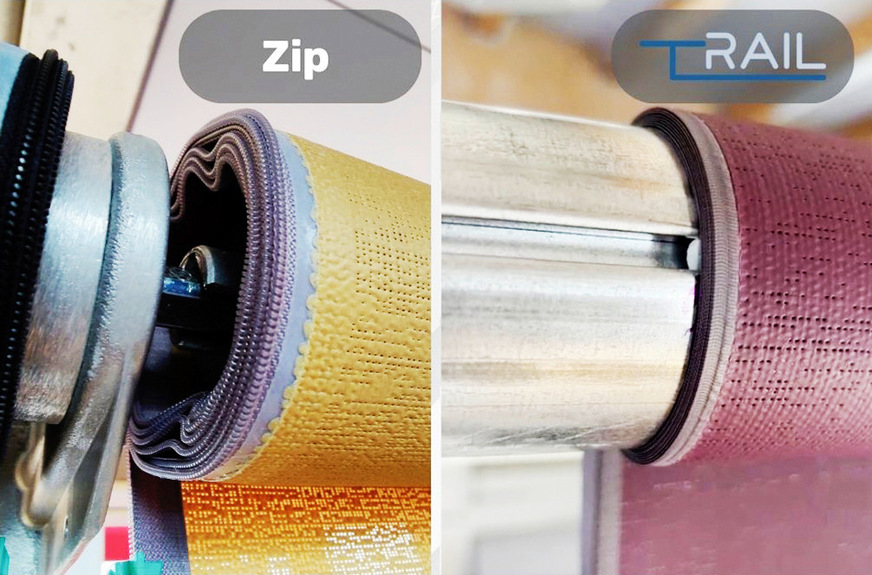
Gluetex / Jentschmann
Considerable space savings
However, as the T-Rail is not thicker than the fabric, there are no different windings in the area of the side seam. This significantly reduces the winding diameter. This in turn saves a considerable amount of space in the housing. The cloth shaft also no longer needs to be offset to make room for an unevenly wound ZIP.
As the fabric shaft is no longer set down, the vertical forces can now also be distributed downwards along the force axis, as it is no longer necessary to cut out the corners of the fabric on the side of the fabric shaft. As a result, the formation of creases in this area is also significantly reduced.
Also interesting: Durable and sustainable fabrics for outdoor sun shading
When the T-rail is unwound, the ‘T’ is positioned in the guide rails and thus provides the necessary lateral support. Here too, the installation space of the inlet or guide rail can be reduced or a higher spring constant can be created. In addition to the obvious advantages above, the T-Rail provides the side seam with additional supporting stability in the vertical direction.