Cradle-to-Cradle in its purest form means that raw materials have been reused in a constant biological or technological cycle without leaving behind environmentally harmful substances and waste. The construction industry is one of the sectors where this principle is currently being debated most intensively. With good reasons: An estimated 8 % of global CO2 emissions are generated during the production of cement. If the cement industry was a country it would be in 3rd place where global CO2 emissions are concerned behind China and the United States. Half of this is emitted during the chemical process, this proportion could thus also not be reduced to zero through production using renewable energy. The construction boom consumes the largest share of natural resources worldwide and, as a result, mineral construction and demolition waste also constitutes the largest waste stream. Natural building materials such as sand and gravel are becoming scarce and their uncontrolled extraction results in considerable environmental impacts in a lot of places.
The best of both worlds: Wood-concrete hybrid construction method
For many architects, the renewable raw material of wood is considered to be one of the key adjustable parameters to reduce the construction industry’s CO2 emissions. On the one hand wood is a natural carbon sink: moreover, much less energy is required during the processing of wood than when manufacturing cement and reinforced concrete. Sustainably cultivated and processed in a recyclable manner, wood is ultimately a valuable resource depot in accordance with the cradle-to-cradle principle.
See also this article: Flats for the future - integrated blinds are the key
In the 22nd district in Vienna one of the tallest wooden towers in the world is on the brink of its final completion. HoHo Vienna, designed by the architect’s office Rüdiger Lainer und Partner, is becoming the landmark of one of the largest urban development projects in Europe, the aspern Seestadt. The three-part main complex consists of the 84 metre high tower comprising 24 storeys. Two additional towers with 15 and 9 storeys are docked against it ensuring the buildings mutually support each other. Furthermore, there is the 6 story adjoining building, the HoHo Next. On the HoHo Vienna plot with its rental area of some 19,500 square metres there is space for a hotel as well as restaurants, offices, serviced apartments and a fitness area.
What about fire safety in this wooden building?
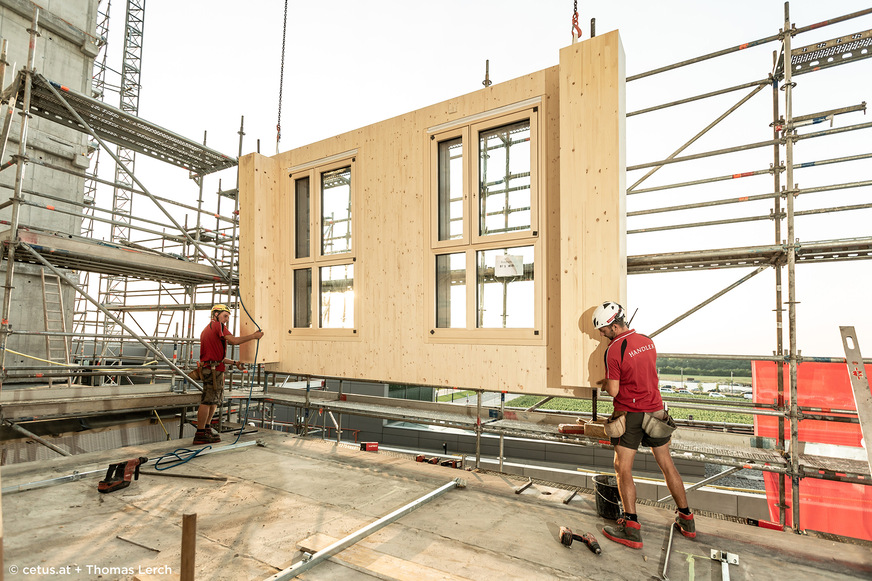
Edgetech
The HoHo Vienna was erected as a wood-concrete hybrid construction. For fire safety reasons, the interior of the building consists of a solid reinforced concrete core containing staircase, elevators and supply shafts. Solid wood structures that are prefabricated in series are arranged around the concrete core. Due to the fire protection requirements that apply, the wooden facade was additionally boarded with fibre cement panels made of natural raw materials. The wall and ceiling elements made of spruce wood remained unclad on the inside.
All in all, the HoHo Vienna achieves a proportion of timber of almost 74 % from the ground floor upwards and, according to Caroline Palfy, project developer and managing director of cetus Baudevelopment GmbH, it saves 2,800 tonnes of CO2 equivalents compared to a conventionally constructed building of the same type and size. One can add to this the short transportation routes due to the fact the wood is exclusively derived from sustainably managed, native forests; one of the requirements for the LEED Gold Certificate. Caroline Palfy states: “The entire timber consumption for the HoHo Vienna re-grows in Austrian forests in just one hour and 17 minutes. 26 million cubic metres of the 30 million cubic metres of wood that re-grows annually in Austria is used. The remaining 4 million cubic metres remain in the forests and constantly increase the country’s stock of timber. This means that 1 cubic metre of wood re-grows every second.”
The wall elements are an example of impressive teamwork
Floor-to-ceiling, double-leaf window elements were originally planned. However, the structural requirements in terms of the resistance to driving rain and wind necessitated a rethink, and the window manufacturer Katzbeck, in collaboration with Holzforschung Austria (Austrian Wood Research Institute), thus developed a solution consisting of two-leaf spruce wood aluminum windows with mullions, a fall protection device and divided lower sash lights. Some 1,100 triple glazed heat protection units with UNIGLAS Top pure FLS were supplied by Petschenig glastec GmbH from Vienna for the facades. The outer pane is laminated safety glass for sound engineering reasons, the inner is single-pane safety glass. Hanspeter Petschenig selected Super Spacer T-Spacer Premium Plus as the warm edge. The insulating glazing thus achieves a Ug value of 0.5 W/m²K which is outstanding from a thermal energy perspective and the glass edge compound scores highly with a Psi value of 0.033 W/mK. The Uw value for the entire window is 0.78 W/m2K, the total solar energy transmittance level is 49 %.
The next prefabrication step was performed at Hasslacher Norica Timber, where the windows were inserted into the wall elements made of cross-laminated timber before the general contractor Handler assumed the final assembly of the complete facade construction. The wall elements were supplied just-in-time, hoisted using a crane and mounted. The U-value of 0.182 W/m2K of the opaque wall elements that are clad with Eternit fibre cement also reflects the good thermal insulation properties of the building.
Economic and space-saving series manufacture
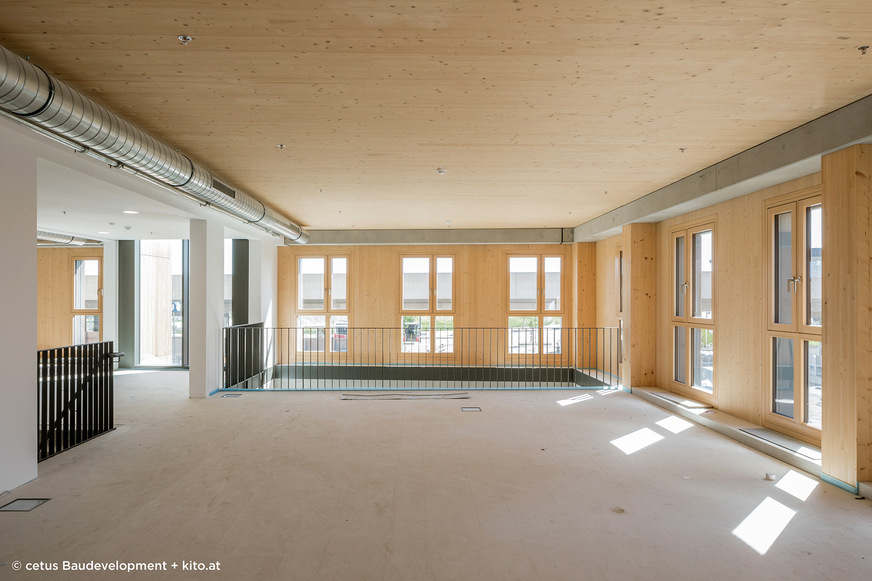
Edgetech
The international high-rise timber construction sector has been boosted by the advent of intelligent precast modular systems. The modular construction principle of the HoHo Vienna impresses through its simplicity. The high degree of repetition of a few solid wood components offers not only cost security, but also the advantage of short construction times due to the fact they can be serially prefabricated irrespective of the weather. The structural engineers at RWT Plus, under the leadership of Richard Woschitz, developed a system node specifically for the Hoho Vienna, which form-fitted the prefabricated elements of the wood-concrete composite ceiling, wooden column, beam and wall element – with virtually no metal connections due to the fact welding work is almost out of the question in a wooden house.
The elaborate technical preliminary tests with regard to fire protection, sound proofing and wind suction loads are also groundbreaking for follow-up projects. According to Holzforschung Austria the window construction and the wall element withstand wind forces of 4,425 Pa without any difficulty.
Is there even an alternative to the warm edge?
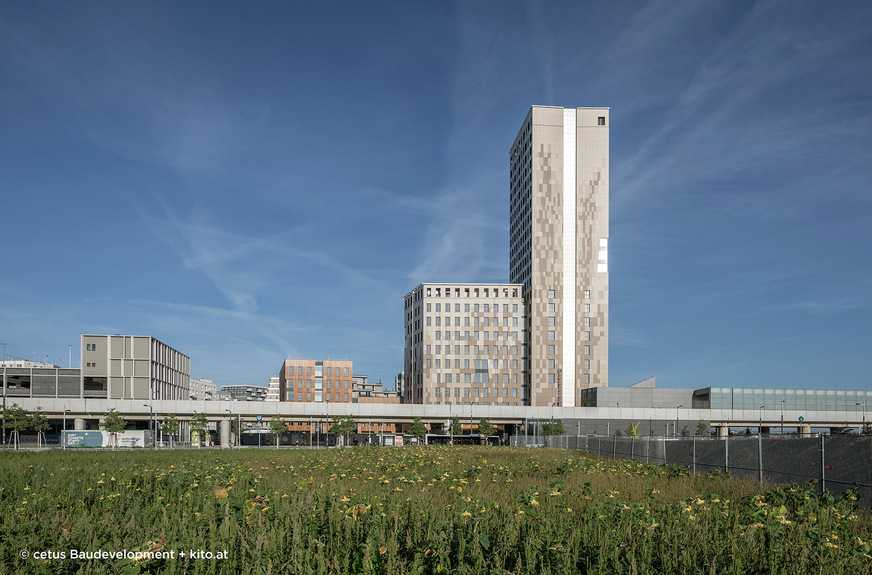
Edgetech
"Of course, the question of whether one should install a thermally separated window edge seal, i.e. a warm edge, does not arise in a sustainability project such as Hoho Vienna," explains Hanspeter Petschenig, Managing Director of Petschenig glastec GmbH, "due to the fact such low heat transfer values as seen in HoHo Vienna cannot be attained in any other way." In combination with the flexible material based on silicone foam, the flawless, tight edge seal also reduces the strains caused by pumping effects and the high wind loads at a height of 84 metres.
Also interesting: Super Spacer for the Eiffel Tower in Paris
However, flexible spacers also offer huge advantages for the production of insulating glass due to the cost savings they bring about. The Super Spacer spacers are controlled by robots and precisely applied from the roll down to the last millimetre at Petschenig glastec GmbH in Leopoldsdorf. “Our automated insulating glass line guarantees that we can produce on schedule and economically”, states Hanspeter Petschenig.
For a bigger picture of what the aspern Seestadt is and will look like once completed, check out this video: