"We do not build nice, small buildings," architect Zaha Hadid told the British Guardian newspaper in 2013, referring to mundane, rectangular structures. For "The Opus", a 21-storey building at the world's most popular architectural playground in the Burj district of Dubai, Hadid had the vision of a cube hollowed out from the inside and to seemingly float above the ground floor. And indeed, like an ice cube that is melting away under the hot desert sun, "The Opus" also provides people inside the building with free views of the surrounding architecture: the Dubai Water Canal, the new opera house as well as the Burj Khalifa and the Dubai Mall. The building accommodates a 5-star hotel, restaurants, office space and luxury apartments.
“The Void“: An engineering masterpiece
After Zaha Hadid had unveiled the design, the "Dream Tower" immediately landed on the top ten wish list of leading industrial companies. Daniel Zhang, Edgetech/Quanex Sales Manager for China, explains the fascination it held for architects and facade builders: "The Opus" was a Black-Box project. At the start no-one was able to say how the organic glass facade, based on Hadid's ideas, covering an area of some 6,000 square meters, could be made to completely appear as a flowing surface. The building as it now stands is an all-encompassing, engineering masterpiece. Each of the 4,544 glass units for the dark blue glazed void is a custom-made individual item, and what’s more the vast majority of them consist of curved double-glazed insulating glass units with irregular shapes. This meant automated application was out of the question for our range of spacers. Nor could a rigid spacer be used, which does not bend without kinks and which certainly cannot be freely moulded. Only a flexible spacer was able to meet the requirements in terms of impermeability and appearance. In hot climates in particular, a warm edge must achieve outstanding levels of performance over decades in order to hermetically seal the space between the panes. Due to the thermal interaction between hot sunlight and shadows, strong mechanical forces permanently act on the edge compound due to the movement of the glass.
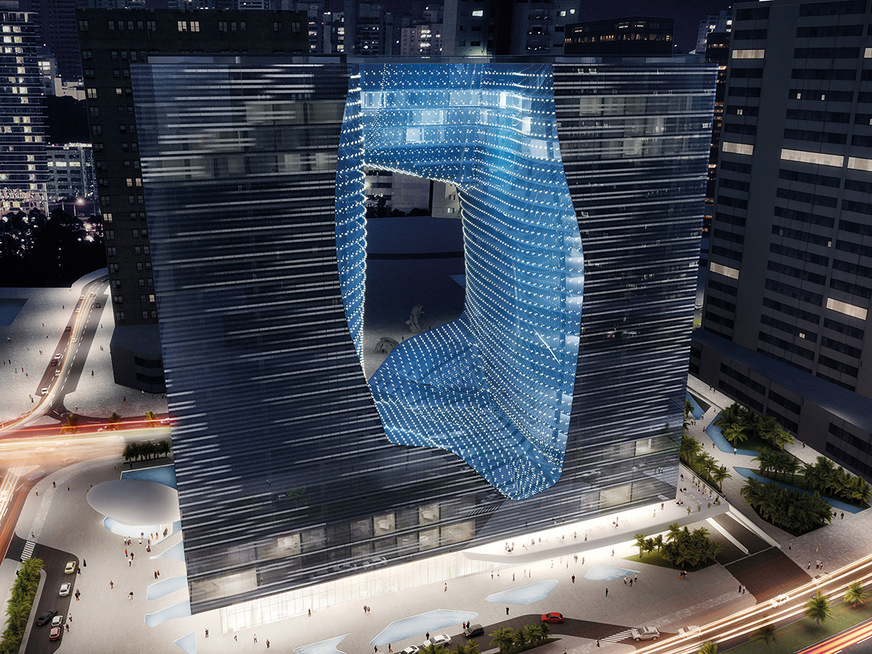
Zaha Hadid Architects
[Warm edge technology for Vienna]
By day, the facade reflects the sky, sun, water and the futuristic architecture. At night, on the other hand, "The Void" is illuminated with LED installations. To this end, LEDs that can be individually controlled were installed in each glass panel. The transparent facades of the two rectangular reinforced concrete towers are made of double-glazed insulating glass with a UV coating and printed coloured layers of different sized dots. On the one hand, they imbue the facade with a unique vitality, on the other hand, they reflect the light and thus reduce the levels of solar input and glare. Teams from different specialist disciplines such as facade builder Alu Nasa, consultants from Koltay Facades in Dubai, Pilkington Glass, the insulating glass manufacturer Shennanyi and also the spacer supplier Edgetech have contributed their collective expertise to the realisation of the "Void". The lower end of the void is bordered by a freely formed glass roof over the multi-story atrium. At the upper end of the building, at a height of 71 metres, the towers are connected by a nearly 38 metre long, elegantly curved and earthquake-proof bridge, made of curved double-glazed insulating glass units, double curved aluminium frames and steel. This part of the building weighs 1,000 tonnes on its own. 3D modelling that is accurate down to the last millimetre of the primary and secondary steel construction, curved aluminium profiles, fastening elements and glass units constituted the basis for all suppliers involved in the project. More than 10,000 individually curved aluminium profiles were supplied from Denmark and the Netherlands, the glass units were produced in three factories in China, and ultimately the entire 3D puzzle had to be precisely pieced together on the construction site.
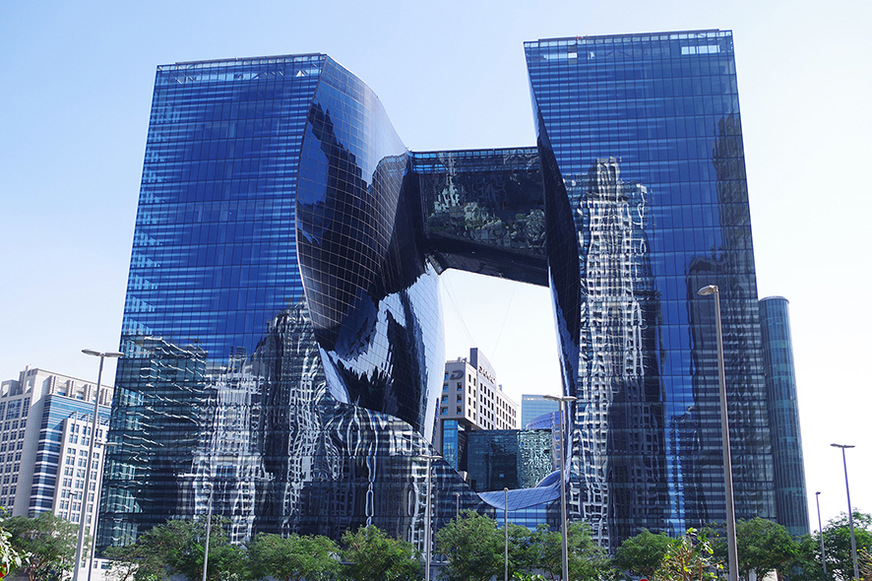
Zaha Hadid Architects
A glass mix a long time in the making
Even the selection of the right glass was preceded by a lengthy decision-making and modelling process. By contrast with flat panes of glass, no technical values exist in relation to the compressive strength, tensile strength and flexural strength for curved panes of glass. Due to the fact the glass curvature and glass thickness affect the flexural rigidity for their part, the solar thermal loads and the maximum energy absorption up to breakage, the minimum bending radii as well as the maximum bending angles for each insulating glass unit had to be calculated. In addition, the glass structure had to ensure that the solar input remained below a certain limit to prevent dangerous levels of reflected radiation that could lead to thermal breakage on the glass facades opposite. In the end, a mixture of a few flat and single bend glass units, as well as hot and cold-bent double-glazed insulating glass units was installed.
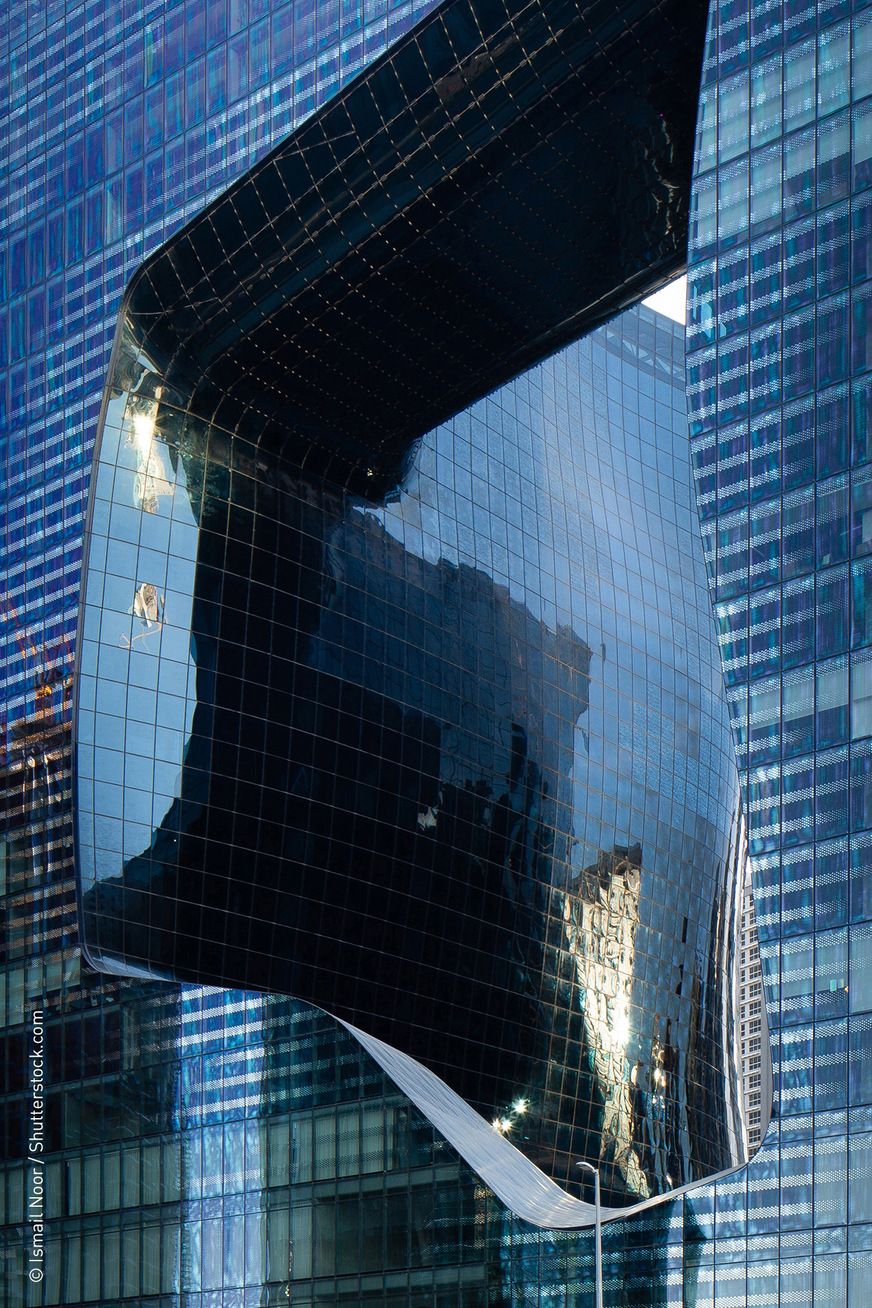
Zaha Hadid Architects
[How SMEs can benefit from automation]
Because in a hot climate such as prevails in Dubai, the thermal load for glass is much higher than in more temperate zones, and the dark glass units also absorb a great deal of energy, the glass should be as tempered as possible - a process that had not yet been industrially tested for curved insulating glass units up to this point in time. Chemically tempered, hot-bent glass was too expensive. Therefore the insulating glass manufacturer Shennanyi developed a technology specifically for the combined hot bending and tempering of the glass whereby the insulating glass units are heated to 700°C, tempered following the moulding process and cooled with the aid of compressed air nozzles to increase their breaking strength. The units consisting of 8 mm Low-E (coated on the inside), a 16 mm cavity between the panes, 6 mm clear glass, a 1.52 mm PVB colour laminate and once again 6 mm of clear glass were constructed by Pilkington China. In order to save costs, the number of hot-bent elements was reduced to a minimum and as far as possible cold-tempered tempered insulating glass was used, and thus one which could be manufactured economically.