Narrow face widths of windows are becoming increasingly popular today. They stand for modern design and at the same time conjure up more daylight in the rooms. But the production of slim profiles for more daylight also poses challenges for machine manufacturers and suppliers: How can the narrow profiles be clamped? How do you ensure high machining quality and precise joints?
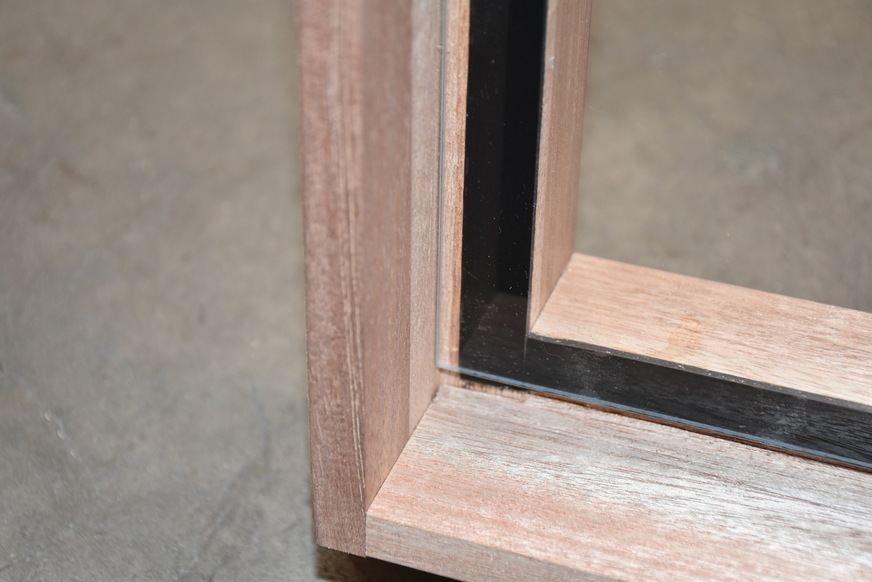
Daniel Mund / GLASWELT
These are the questions that window manufacturers are asking machine manufacturers and suppliers in the industry today. And rightly so, because such innovative window systems can only be created if the manufacturers of machine technology and suppliers continuously work closely together.
20% more glass: window systems in integral design
An example of this cooperation are windows in integral construction. Slim profiles ensure maximum light with a visually elegant narrow view. The basis for this is adhesive technology. It ensures a secure bond between the pane and the frame.
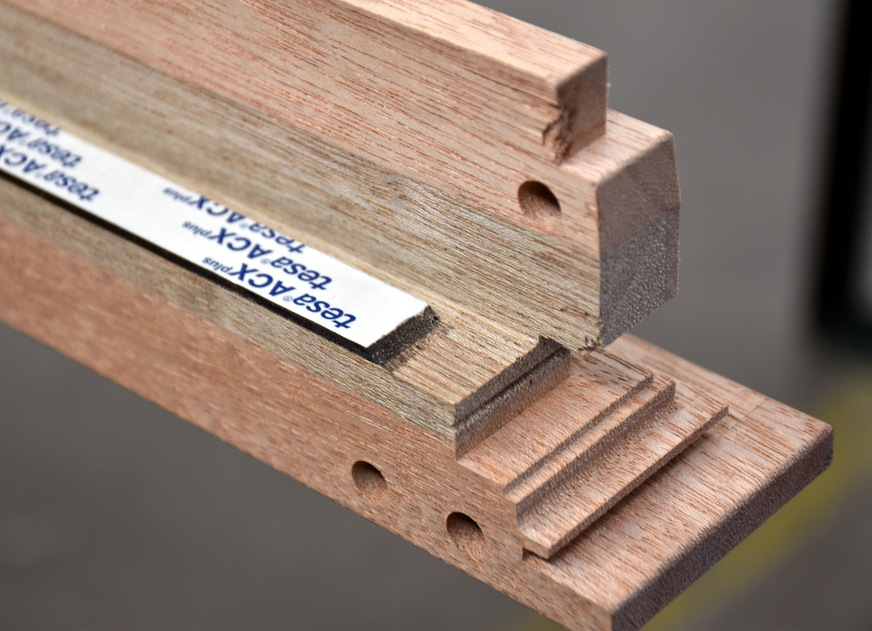
Daniel Mund / GLASWELT
See also this article: BarteltGlasBerlin no longer plastic uses plastic packaging
Such an integral window was presented for the first time at the window day of the Homag meeting. Volker Schmieder, technical sales manager at the machine manufacturer Homag, is responsible for the concept: "We have developed a wooden window system that is primarily intended to compete with PVC windows. The aim is not only to be able to produce cost-effectively, but at the same time to be able to exploit technical advantages and also to score points visually with the new window.
The adhesive technology is crucial here: this is where adhesive tape specialist tesa comes into play. Window manufacturers can thus bond the insulating glass to the raw wood (the adhesive tapes are applied to the raw wood and then painted over). tesa application engineer Matthias Weets: "A special bonding agent, in conjunction with the high-performance adhesive tape from the tesa ACX plus 707x series, ensures the high bond strength. With this adhesive system, resistance class RC2 can be achieved."
Did you know about the new 68 mm Mira TWT wood-aluminium window from Gutmann?
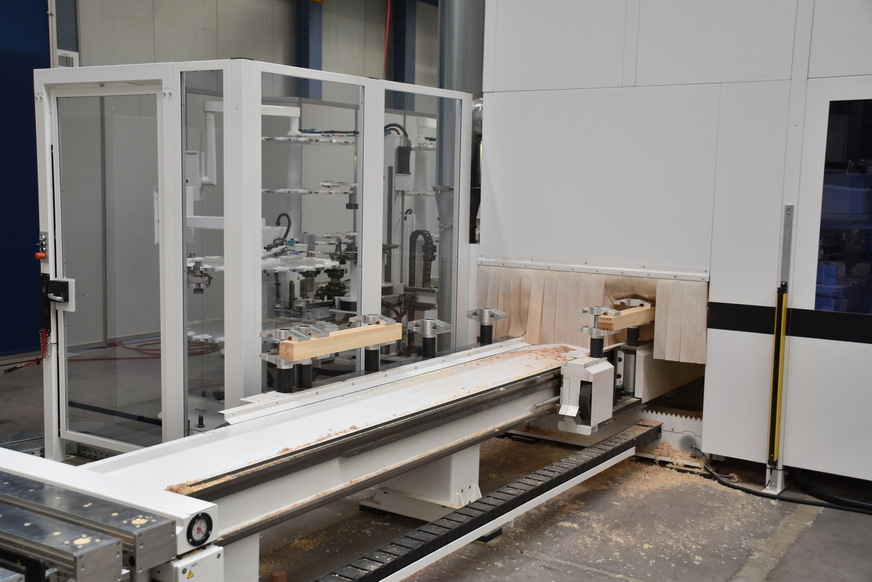
Daniel Mund / GLASWELT
The development team tested the concept on the window test stand at Siegenia. The basic system has therefore been developed and test certificates are available. An important system partner was Gutmann from Weissenburg, who supported the window experts in important design issues. Now the experts from Homag and tesa say they are still 'fine-tuning' the system as far as its practical introduction is concerned. They are also looking for window manufacturers who want to be involved in this fine-tuning.
As far as the potential of the window concept is concerned, Schmieder, in conversation with GLASWELT, is confident that it could generate a market share of 1 per cent. In his opinion, in the medium term the majority of wood-aluminium window systems will be equipped with corresponding adhesive technology. There is also potential in the wooden window sector: The process used can be transferred to existing systems.
What are the general properties of this composite window?
More light in the room: Narrow sash profiles allow larger glass surfaces. This results in up to 20% more glass and thus more daylight compared to conventional systems.
Modern look: Flush on the outside when installed in the reveal, the frame is practically invisible. This creates a modern, reduced look.
Low maintenance: The pane and frame are fixed and cannot be moved. The sash remains stable, the effort for later readjustment is significantly lower.
Increased burglary protection: The pane cannot be practically separated from the sash frame. It stiffens the frame. The frame yields less during an attempted break-in.
High thermal insulation: The narrow frame enables the best U-values of the windows.
Simple production: The profiling of the frame parts is simple and requires less machining and use of wood and therefore lower tooling costs. The gluing ensures the statics of the sash, the corner connection can be kept simple. The perfect complement to this is the screwed corner: the individual parts can be completely surface-finished and the frame assembled without a press.
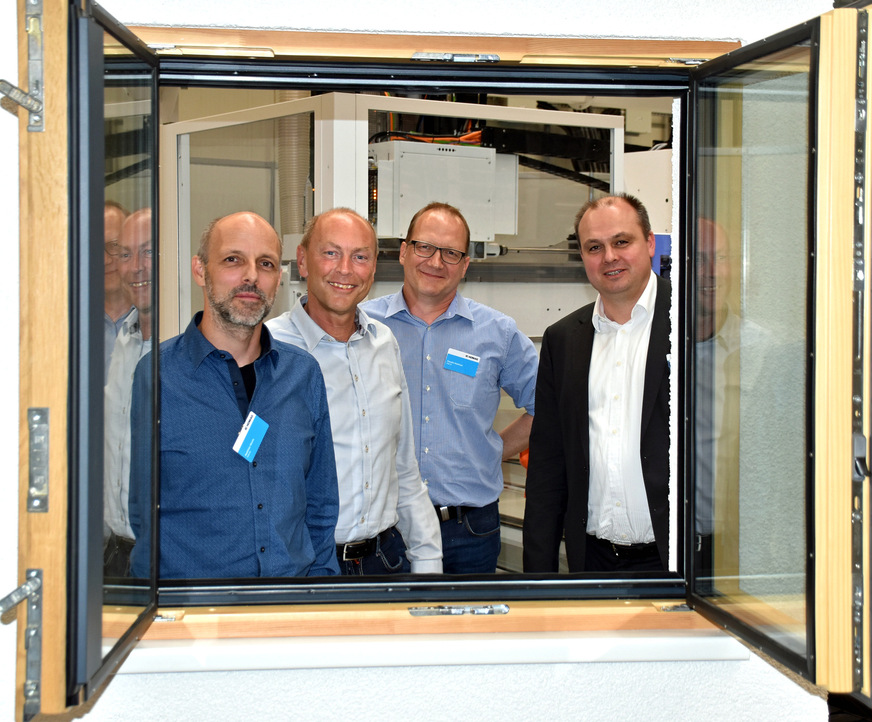
Daniel Mund / GLASWELT
Did you know about the GW News newsletter?