The idea of using vacuum lifters on construction sites is not new. There are numerous devices that can be hung on cranes or even mounted on forklifts or telescopic stackers to move loads on construction sites.
Experienced window and façade constructors know, however, that a successful installation of elements is decided on the last centimetres during insertion. Here, common equipment often lacks the necessary precision and 360-degree 3D movement.
In addition, window elements have to be inserted from the inside to the outside. This is also the reason why "glass manipulators" or "glass robots" are often used, which pick up the glass elements in the building and help to place them.
Up to now, there has been no other option than to transport elements and machines into the building at great expense. This is still possible in the shell of the building. However, if the building is already finished and possibly has raised floors for IT and communication technology, the weight of the machines in combination with the glass usually exceeds the load-bearing capacity of the floor and its covering.
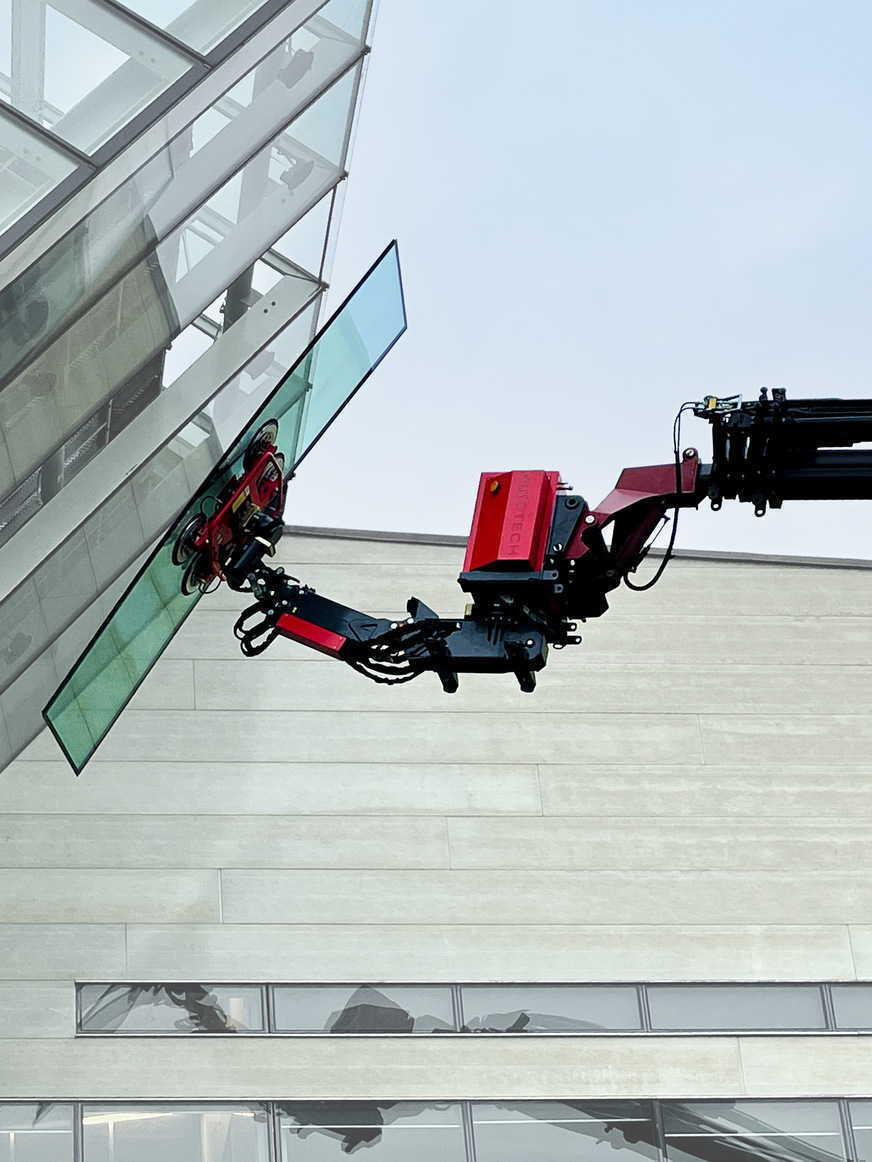
euroTech
Outdoor installation is the ideal solution
It should also have a powerful vacuum lifter that can handle heavy loads of over 500 kg. Thirdly, a self-sufficient power supply and its own hydraulic power unit are required in order to be able to work close to the final position with millimetre precision.
The ideal way to install glass and façade elements quickly and easily with as little labour as possible is to use outdoor installation. This requires an assembly module that combines four elements into a functioning unit. First of all, the module should be compatible with a standard lifting device with a corresponding outreach, such as those available from many construction machinery rental companies (e.g. a telescopic forklift).
Finally, an intuitive 3D control and bearing system enables smooth movements in all directions.
See also: Battery-powered hand-held vacuum handling devices – a handy solution
Originally, the et-Litocran700 was designed as an autonomous add-on module consisting of the vacuum lifting device "eT-Hover-univac" and its own telescopic arm, which can perform 360-degree movements on the last centimetres.
The load capacity is designed for 700 kg. The module's own power and hydraulic supply with its own remote control makes the unit independent and flexible. It can be attached to a telescopic forklift as well as to a crane.
Time and cost pressure in construction projects
A construction site project in the immediate vicinity of euroTech's headquarters in Rosenfeld showed just how operational the eT-Litocran700 really is.
By June 2023, a representative administration building and a modern production facility covering more than 37,000 m2 will be built.
The tight schedule posed a real difficulty for the commissioned window and façade manufacturers. The delivery of specially manufactured window elements was delayed. When the eagerly awaited elements finally arrived, it was time to install them.
On the one hand, it had to be ensured that the custom-made elements would not be damaged under any circumstances during installation, and on the other hand, there was a tricky installation situation. The installation site was under a roof at a height of 20 metres. The window could not be placed at a 90-degree angle to the façade, because the window opening was to the right of it, below the roofing.
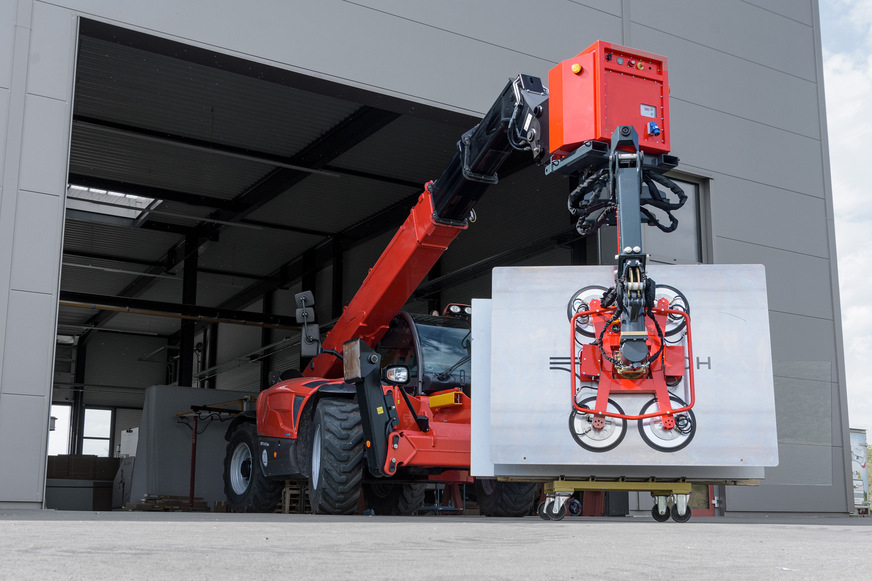
euroTech
A crane was therefore out of the question. It would have been conceivable to erect scaffolding on which a lifting device could then be placed, but this would again cost valuable time. In addition, a light shaft in the underground car park, which was located directly below the installation site, caused headaches.
The managing director of Saxonia Glas- und Fassadenmontage GmbH was aware that euroTech had a telescopic loader attachment module, the eT-Litocran700, which is precisely suited to such challenges. He had been toying with the idea of testing the eT-Litocran700 for some time.
Now the moment had come. He turned to the neighbouring euroTech headquarters and received immediate support. The eT-Litocran700 was quickly mounted on the borrowed telescopic forklift. The telescopic forklift positioned itself at a distance from the building's roof and the light shaft and transported the Litocran to installation height.
Also interesting: Installing curved facade elements for a modern office building
Then the Litocran fine control for placing the element was done by an operator at the separate remote control. Carefully, he approached the window opening with the 400 kg pane. The clearance for installation was only 10 mm on each side. However, the eT-Litocran700 proved its operational capability under the most difficult conditions and reacted with millimetre precision to every control impulse in all directions.
The tricky challenge was solved in no time. Saxonia Managing Director Hannes Sachse was relieved: "We mastered the task with the Litocran in record time with minimal financial and personnel effort. The Litocran baptism of fire on our first job was passed with flying colours!"
For details on the installation, see here: