This time in Düsseldorf, Forel has presented a fully automated insulating glass line for thermoplastic spacers as well as the latest automation solutions.
Developed according to the principles of Industry 4.0, the highly automated IGU line can be controlled from a single workstation and offers high productivity, precision and quality, according to Forel.
The line is loaded automatically via the Art. SS Sorting System, Forel's storage and retrieval system for managing jars in production. The system is capable of automating production control software and programming.
Automation in the IGU line
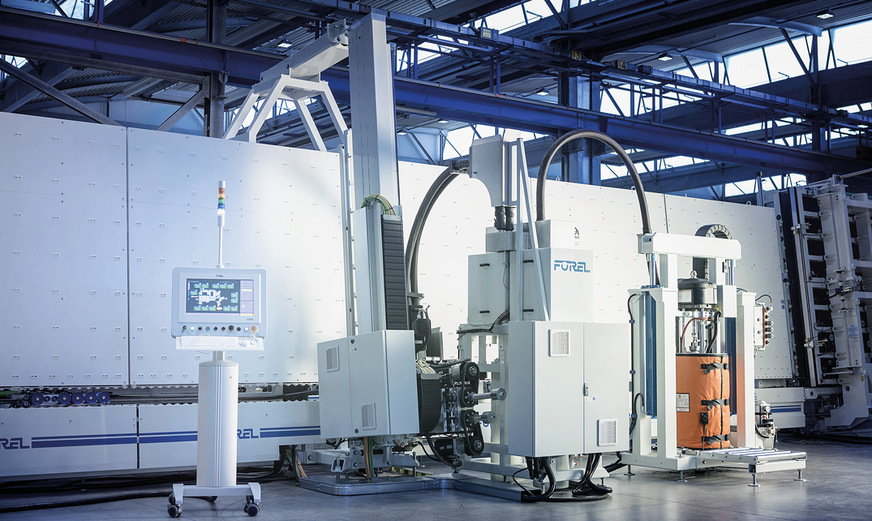
Nudesign srl / Forel
At the heart of the high-tech IGU line is the Art. TA Thermoplastic Applicator, designed for ease of operation and continuous productivity, which precisely extrudes and applies thermoplastic spacers.
Automation of the applicator is said to be key to productivity with options to automatically change profile thickness, corner radius and viscosity by simply changing the working parameters from a PC.
The thermoplastic spacer is continuously processed through the system via a tandem pump. The system contains two precision accumulators that feed the application head.
This configuration proves to be advantageous: an empty vat can be changed without interrupting production, which avoids downtimes.
For the thermoplastic spacer, the temperature is automatically monitored and controlled during the extrusion process. And a special option has been developed for the AP coupling press, which makes it possible to process rigid and thermoplastic spacers.
The Art. SR "High Tech" sealing robot takes over the last step in the production process, which is then completed by the GU, an automatic unloading system. After sealing, the finished ISO units are taken over by a vertical pick-up table, which gently places the units on waiting transport trolleys.
The model Art. GU, which has also been on show at glasstec, has a unique system that enables the safe storage of both rigid profile sheets and sheets with thermoplastic spacers.
Furthermore, Forel also showed machines for processing traditional rigid spacers: the profile bending machine Art. PB, the desiccant loader Art. DF and the manual butyl applicator Art. MB. The profile bender has been enhanced with a number of innovations for bending plastic spacers with a "warm edge", while the patented Smart Arm technology allows it to offer 90° corners.
Vertical edge processing
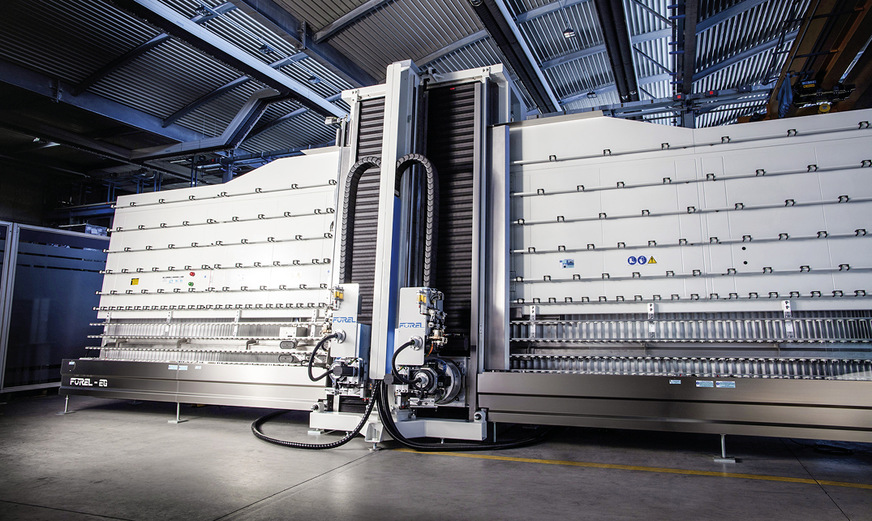
Nudesign srl / Forel
For the first time, the entire product range for vertical edge processing has been presented in one place. This line for vertical consists of the Art. EM edge processing line, the Art. DM drilling and milling centre and the Art. VW washing machine.
This combination of machine modules can perform a variety of processing tasks for both monolithic and laminated glass, including edging, grinding, polishing, milling and drilling, which is rounded off with final washing.
The three inline machines are capable of simultaneously processing different glass sheets, managed via onboard software, which increases productivity and quality. The Art. EM and Art. DM modules are designed for stability and precision.
The "sister line" in edge processing, designed for high capacity, consists of the Art. EG edge processing line and the washing machine Art. VW. This line is specifically designed for glass processors who are looking for a machine that removes sharp edges and micro-fractures from glass with minimal set-up and maximum performance.
All Forel vertical edging lines use diamond-coated grinding tools as standard, ensuring a high quality of finish and a long service life, Forel says.